What Causes Tap Breakage & How To Solve
Why do our tap bits keep breaking? The breakage of tap bits is indeed a complex issue involving multiple factors. There is no standard answer to this question. Factors such as workpiece material, tool material, tool design, heat treatment, tolerance level, machining accuracy, coating quality, and many others can all affect the durability of tap bits. Today, let’s delve into the reasons for tap bit breakage and discuss potential solutions.
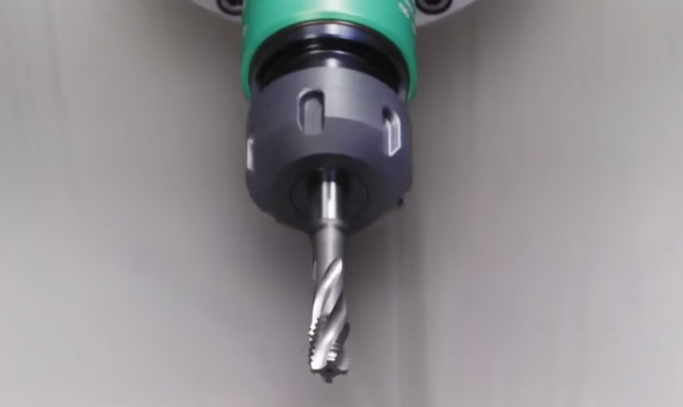
Reasons for Tap Breakage
Workpiece Material:
Excessive Hardness: If the workpiece material is significantly harder than the designed cutting capability of the tap bit, it will encounter excessive resistance during cutting, leading to breakage.
High Toughness or Brittleness: Some materials may exhibit high toughness or brittleness, making it difficult for chips to break off or causing cracks on the workpiece surface, which both increase the load on the tap bit and may trigger breakage.
Impurities or Inclusions: Impurities or inclusions in the workpiece material can serve as stress concentrators, accelerating the wear or breakage of the tap bit.
Tool Material:
Mismatch: If the material of the tap bit is not compatible with the cutting performance required by the workpiece material, such as insufficient hardness or poor wear resistance, it can lead to rapid wear and breakage.
Quality Issues: Defects in the tool material itself, such as cracks or pores, can also reduce its durability.
Unreasonable Geometric Parameters: Inadequate design of cutting angles, rake angles, and clearance angles can affect the distribution of cutting forces and the generation of cutting heat, increasing the risk of breakage.
Insufficient Strength: The cross-sectional dimensions and flute designs of the tap bit may not meet the requirements for cutting strength, leading to breakage.
Heat Treatment:
Improper Heat Treatment: For example, excessively high quenching temperatures or insufficient tempering can result in uneven internal structure and residual stresses in the tap bit, reducing its toughness and strength.
Improper Hardness Control: Excessive hardness can increase brittleness, while insufficient hardness reduces wear resistance, both of which can contribute to breakage.
Tolerance Level and Machining Accuracy:
Excessively Tight Tolerances: If the tolerances for workpiece holes or threads are designed too tightly, the tap bit may experience excessive squeezing and friction during cutting, leading to breakage.
Low Machining Accuracy: Factors such as poor machine tool accuracy or unstable fixtures can cause vibration or deflection of the tap bit during cutting, increasing the risk of breakage.
Coating Quality:
Coating Detachment or Wear: The primary role of coatings is to reduce friction, lower cutting temperatures, and improve wear resistance. Poor coating quality or significant wear and tear during use can directly impact the durability of the tap bit.
Poor Adhesion Between Coating and Substrate: Insufficient bonding strength between the coating and the tool substrate can also lead to coating detachment or substrate cracking.
How to Solve Tapping Tool Breakage
1. Optimize Tool Selection and Usage
Select the Appropriate Tap: Choose the right tap material based on the workpiece material’s hardness and toughness. Options include cobalt high-speed steel taps, carbide taps, or coated taps. Ensure that the tap’s geometric parameters, such as cutting angle, rake angle, and relief angle, are designed to improve cutting efficiency and durability.
Inspection Before Use: Check the tap for cracks, wear, and other defects to avoid using problematic tools. Confirm that the tap’s precision and tolerance levels meet processing requirements.
2. Improve Cutting Conditions
Adjust Cutting Parameters: Set the cutting speed, feed rate, and cutting depth appropriately based on the workpiece material and the tap characteristics. Avoid excessive cutting loads. Control the use of cutting fluid to ensure sufficient cooling and lubrication in the cutting area, reducing cutting temperature and friction.
Optimize Bottom Hole Diameter: Select the appropriate bottom hole diameter to avoid excessive cutting load caused by a too-small diameter. Generally, the bottom hole diameter should be slightly larger than the tap’s nominal diameter.
3. Enhance Processing Accuracy and Stability
Improve Machine Tool Precision: Ensure that the machine tool’s precision and stability meet processing requirements to avoid cutting vibrations and deviations due to insufficient precision. Use suitable fixtures and clamping methods to ensure the workpiece’s stability during processing.
Control Processing Environment: Maintain a clean and stable processing environment, avoiding temperature, humidity, and other environmental factors that could affect processing accuracy.
4. Improve Tool Maintenance and Care
Regular Tool Maintenance: Regularly clean, inspect, and maintain taps, replacing severely worn tools promptly. When storing tools, avoid collisions and moisture, keeping the tools dry and clean.
Enhance Operator Skills: Strengthen operator training to improve their skills in using tools and adjusting cutting parameters. Increase operators’ sense of responsibility and safety awareness to avoid breakage accidents caused by human factors.
5. Use Special Removal Methods
Welding Method: Weld a handle or hex nut to the broken section of the tap, then slowly turn it out. Pay attention to welding techniques and applicability.
Specialized Tools: Use specialized tools such as broken tap extractors. These tools use electrochemical corrosion or mechanical force to remove the broken tap from the workpiece.
Other Methods: Consider methods like EDM (electrical discharge machining) or wire cutting, but be mindful of their impact on the workpiece and threaded hole.
How to Correctly Choose a Tap
Choosing the right tap for machining hard workpieces is crucial, balancing machining effectiveness and cost control. For such workpieces, high-speed steel (HSS), carbide taps, and coated taps are commonly recommended due to their high hardness and wear resistance. To further enhance tool life and cutting performance, taps with TiN or TiCN coatings can be chosen. When making a selection, it’s essential to balance quality and price; it’s not always necessary to choose the most expensive product but rather to decide based on actual machining needs and budget.
Different tap designs are suitable for different machining situations. Straight flute taps are ideal for through-hole machining, while spiral flute taps are more suitable for deep and blind holes. Forming taps are mainly used for machining soft metals and are particularly suitable for thin-walled workpieces. Machine taps and hand taps are respectively used for machine tapping and manual tapping. The specific application scenario should be considered to ensure optimal machining results. Additionally, reasonable selection of cutting parameters and the use of appropriate cutting fluids can significantly improve machining efficiency and extend tool life.
While pursuing cost-effectiveness, it is also necessary to consider the durability of the tools and potential regrinding needs. For high-volume machining, bulk purchasing might be more economical. In general, when choosing a tap, it is important to comprehensively consider the workpiece material, machining requirements, usage frequency, and budget to achieve the goal of ensuring machining quality while controlling costs.
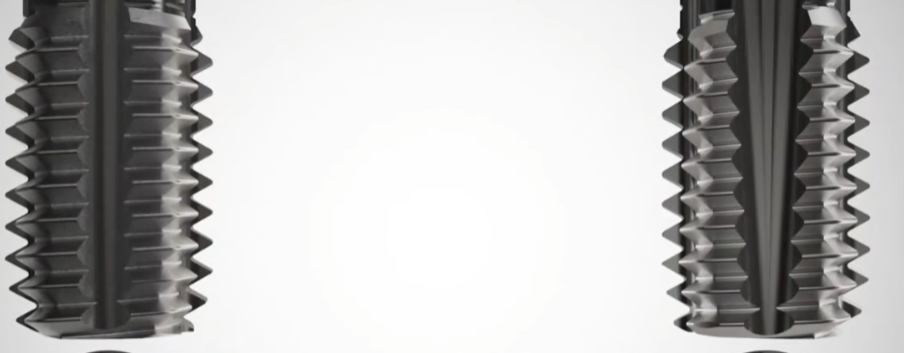
How to Choose the Right Tap for Our Material
First, we need to understand the properties of the material, including its microstructure and whether it has undergone heat treatment. This will directly influence our choice of tap material and hardness. For hard or high-strength materials, taps made from harder materials are typically needed. If the material has been softened, using softer taps can minimize damage.
Second, the material’s specifications and dimensions are also important reference factors. For high-precision machining of small holes, a combination of more taps or finer taps can be used to improve hole straightness. For general rough machining, standard models can suffice.
Additionally, the project’s machining cycle and conditions need to be considered when making a selection. For long-term or mass production machining, the tap’s lifespan and stable performance are critical. Taps suitable for such applications usually feature higher quality structural designs and lubrication methods.