How To Ask Effective CNC Machining Techniques From AI?
What exactly is AI? What impact can its emergence bring to the mechanical manufacturing industry? Will your job position be replaced by AI in the future? AI can bring tremendous changes to the CNC industry and practitioners. The core use of AI actually depends entirely on whether you can guide and ask questions. To get a good answer, the prerequisite is that your question must be rigorous and comprehensive, and you can use text and pictures to ask questions. Today we will discuss suggestions for conventional processing, specific material processing, and machined parts, as well as how to ask AI questions.
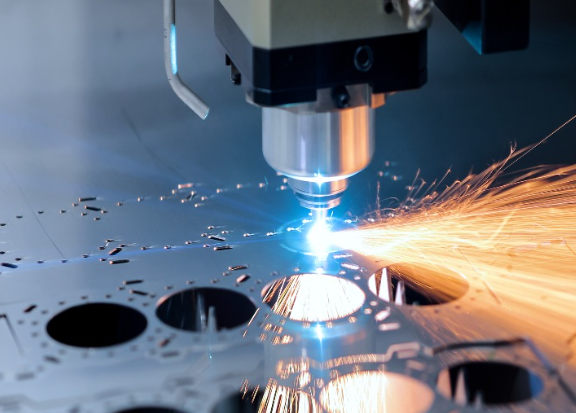
1. Use a 1-10mm hard alloy milling cutter to process 45 steel. How to choose cutting parameters?
Question: If you are a professional construction engineer and use a 10mm diameter coated hard alloy milling cutter to machine 45 # medium carbon steel, how would you choose the parameters for the bottom edge of the milling cutter?
Linear speed=80-120m/min
Feed per tooth Fz=0.05-0.1mm
Cutting depth AP=10% -20% D
Cutting width AE=50% -70% D
2. 10mm hard alloy milling cutter is used for dynamic machining of 45 # steel with side edges. How to choose cutting parameters?
Question: If we want to use dynamic machining with tool edge measurement, how should we choose the cutting parameters?
Linear speed=120-150m/min
Feed per tooth Fz=0.1-0.2mm
Cutting depth AP=70% -100% D
Cutting width AE=10% -25% D
3. How to process an aluminum plate with a thickness of 3-500×500 from 15mm to 10mm to reduce deformation?
Question: I want to use a three-axis machining center to machine a 707 integrated aluminum alloy subframe with a length of 500 millimeters, a width of 500 millimeters, and a thickness of 10 millimeters. The current blank thickness is 15 millimeters. Please provide me with some effective clamping methods and process solutions to minimize product size deformation.
Effective clamping method
Vacuum suction cup: The use of vacuum suction cups can effectively fix large areas of workpieces and reduce deformation caused by clamping. For aluminum alloy workpieces, vacuum suction cups can provide uniform clamping force. Placing a layer of rubber pad between the vacuum suction cup and the workpiece can increase friction and protect the surface of the workpiece.
T-slot worktable and fixture: By using T-slot worktable and adjustable fixture, the clamping position can be flexibly adjusted according to the shape and size of the workpiece, ensuring the stability of the workpiece.
Place soft cushion material (such as aluminum foil or plastic sheet) between the fixture and the workpiece to reduce deformation caused by concentrated clamping force.
Customized fixtures: Design and manufacture specialized fixtures that fit the shape and size of the workpiece. Customized fixtures can provide better support and clamping effects, reducing vibration and deformation during the machining process.
Process plan
Pre machining and rough machining: First, perform pre machining on the shape of the workpiece, and machine the thickness from 15 millimeters to near the final thickness (such as 11-12 millimeters). This step can remove most of the material and release internal stress. Perform rough machining with a certain margin (such as 0.5-1 mm) for subsequent precision machining.
Symmetrical processing: Try to use symmetrical processing to alternately process both sides of the workpiece, in order to evenly release internal stress and reduce deformation. After processing one side, flip the workpiece over, re clamp and process the other side.
Precision machining: In the precision machining stage, reduce the cutting depth and feed rate to minimize cutting force and heat accumulation. Use sharp cutting tools and appropriate cutting fluid to reduce cutting temperature and minimize thermal deformation.
Multiple clamping: The workpiece is processed in stages, and each stage is re clamped to ensure the dimensional stability of the workpiece after each processing. Positioning pins and precision fixtures can be used to ensure that the position of the workpiece is consistent after each clamping.
Control environmental temperature: Temperature changes in the processing environment can affect the dimensional accuracy of the workpiece. Maintain stable processing environment temperature and try to avoid sudden changes in workpiece temperature during the processing.
4. What kind of manufacturing process should be used for weakly rigid frame structural components?
Question: You are a professional CNC engineer. For this weakly rigid automotive frame structural component, the material is 7075 aluminum alloy. Please provide me with some process solutions to ensure that the product will not deform as much as possible.
-Preliminary preparation and material handling
Material pretreatment: Heat treat the material to eliminate internal stress as much as possible. Use materials with high stability and choose 7075 aluminum alloy that has undergone sufficient aging treatment.
-Clamping and fixing
Vacuum suction cups and flexible fixtures: Using vacuum suction cups can evenly distribute clamping force and reduce local stress. Using flexible fixtures and customized fixtures, design fixtures according to the shape of the workpiece to ensure uniform support and stable clamping.
T-slot worktable: By using a T-slot worktable and adjustable fixtures, the clamping position can be flexibly adjusted to ensure the smooth fixation of the workpiece.
-Processing technology flow
Pre processing and rough processing: Remove excess material, process the thickness from 15 millimeters to near the final thickness (such as 11-12 millimeters), and release initial stress. Perform rough machining on the workpiece, leaving a 0.5-1mm margin for subsequent precision machining.
Symmetrical machining: Perform symmetrical machining by alternately machining both sides of the workpiece, evenly releasing internal stress, and reducing deformation.
Step by step processing: Process in multiple steps, removing a small amount of material each time, minimizing the amount and force of a single cut, and reducing the risk of deformation.
For thin-walled areas, use small cutting depths and slower feed rates.
-Precision machining
Multiple clamping and repositioning: After each processing stage, the workpiece is re clamped and repositioned to ensure consistent position after each processing. Use positioning pins and precision fixtures to ensure that the position of the workpiece is consistent after each clamping.
Small cutting depth and low feed rate: In the precision machining stage, small cutting depth (such as 0.1-0.2 millimeters) and low feed rate are used to reduce cutting force and heat accumulation.
Tool selection and cooling: Choose sharp hard alloy tools to reduce cutting force. Use cutting fluid for cooling to reduce machining thermal deformation.
-Environmental control
Temperature control: Maintain stable temperature in the processing environment and try to avoid changes in workpiece size caused by temperature fluctuations. During the machining process, stop machining regularly to allow the workpiece and machine tool to cool down and reduce thermal deformation.
-Multiple measurements and adjustments
Measurement and adjustment: After each processing stage, high-precision measuring tools (such as coordinate measuring machines) are used to measure the dimensions of the workpiece. Make necessary adjustments based on the measurement results to ensure the dimensional accuracy of the workpiece.
-Post processing
Stress relief treatment: After processing, the workpiece is subjected to low-temperature annealing or vibration aging treatment to further eliminate residual stress.
-Process recording and optimization
Recording and optimization: Record the parameters and results of each processing, continuously optimize the process parameters and methods according to the actual situation, in order to improve the processing quality and efficiency.
5. Learn more details
Question: Please explain to me some techniques about symmetrical machining and step-by-step machining
Symmetrical processing techniques
Symmetric processing and gradual processing are key technologies for reducing deformation of weakly rigid workpieces. Symmetric processing involves alternately processing both sides or multiple surfaces of the workpiece to evenly release internal stresses in the material and avoid uneven stress distribution caused by one-sided processing. Layered cutting is an important technique in symmetrical machining, which involves dividing the machining process into multiple layers, removing a small amount of material each time, and flipping or rotating the workpiece after each removal to complete the machining layer by layer. Maintaining consistent depth and width for each cutting is another key point in symmetrical machining, which ensures uniform stress release. In addition, designing fixtures suitable for symmetrical machining is also essential. These fixtures need to be accurately positioned after each flip or rotation of the workpiece to ensure the stability and consistency of the machining.
Step by step processing
Gradual processing reduces the amount of single cutting and cutting force by gradually removing materials, thereby reducing the risk of deformation. Using a small cutting depth and low feed rate during each cutting can reduce cutting force and heat accumulation, thereby maintaining the dimensional accuracy and surface quality of the workpiece. Gradual processing is usually divided into multiple stages, starting with rough machining, followed by semi precision machining, and finally precision machining, with a certain margin reserved for each stage for use in the next stage. Repositioning and clamping the workpiece is crucial during the gradual machining process, and high-precision positioning fixtures are required after each stage to ensure the machining accuracy of the workpiece in the next stage. Gradually reducing the cutting amount is also an important technique for gradual machining. When approaching the final size, using extremely small cutting depths for cutting can achieve higher dimensional accuracy and surface quality. Regularly use measuring tools for measurement and monitoring, adjust cutting depth, feed rate, and tool path according to actual conditions to optimize machining results, and use appropriate cutting fluid for cooling and lubrication to reduce heat accumulation and prevent workpiece deformation due to temperature changes. Through these symmetrical and step-by-step processing techniques, the deformation of weakly rigid workpieces during the processing can be effectively reduced, ensuring the dimensional accuracy and quality of the final product.
What do you think of AI’s response? Although AI may not provide you with optimal answers, it provides comprehensive answers and offers you a lot of inspiration and suggestions. As long as we master the methods, we can easily solve your process problems.