CNC Machining: Advantages, Programming, and Setup
CNC (Computer Numerical Control) machining is a subtractive manufacturing process used to produce parts and components made from materials like metals and engineering plastics. Engineers select the appropriate tools for the job and load them along with the material into CNC machines. CNC machining offers many advantages, including greater precision compared to manual machining and the ability to repeatedly produce identical parts. Its high accuracy enables the creation of complex shapes that would be difficult to achieve otherwise.
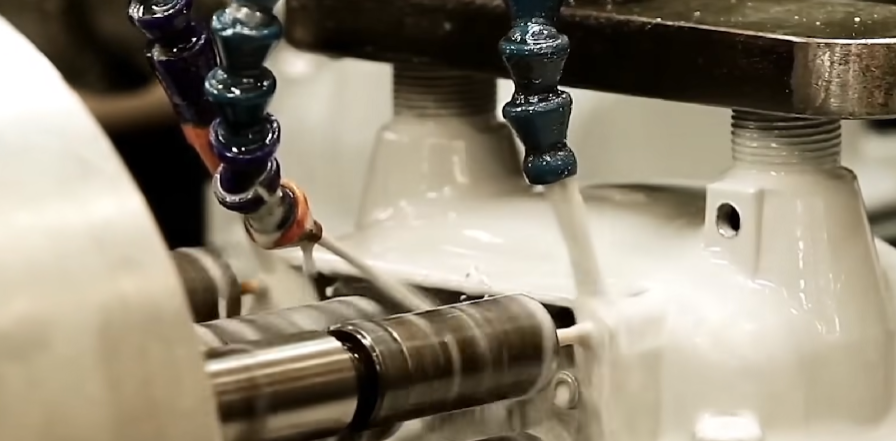
Computer-Aided Design (CAD)
Computer-Aided Design (CAD) utilizes software to assist in engineering design tasks. Unlike traditional hand-drawn designs, CAD allows for product designs in three-dimensional geometric forms, making the process more intuitive and practical. During design, multiple modifications can be made with immediate updates to the drawings, enhancing design efficiency. CAD supports product assembly, cross-sectional and style drawings, and virtual performance validation. Completed designs can be exported into various files needed for manufacturing, such as CNC machining drawings, and are useful for rapid prototyping. Collaboration between designers over networks is facilitated, and design changes can be tracked. Various analyses, such as strength and finite element analysis, are performed to improve product quality.
CNC Programming
CNC programming (Computer Numerical Control Programming) refers to the use of computer software or programming languages to control CNC machines (such as lathes, mills, and drills) for precise machining. CNC programming involves writing code that conveys the machining path, cutting parameters, and feed rates to the CNC device, enabling an automated machining process.
The primary goal of CNC programming is to achieve efficient and precise mechanical processing, widely used in manufacturing, aerospace, automotive, and medical device industries. Through CNC programming, engineers can design and produce complex parts, reducing human error and increasing production efficiency.
CNC Programming Workflow
- Design Drawing: Engineers create a 3D or 2D model of the workpiece using CAD software, serving as the basis for programming and machining.
- Process Selection: Determine suitable machining processes (turning, milling, drilling, cutting) based on the design, and select appropriate tool types, cutting speeds, and feed rates.
- Code Writing: CNC programs use G-code (for controlling machine movement and tool positioning) and M-code (for auxiliary functions like coolant control and spindle operation).
- Simulation and Verification: Before actual machining, use CAM (Computer-Aided Manufacturing) software to simulate and verify the program, checking for collisions and overcuts.
- Program Loading: Upload the verified CNC program to the machine for actual processing.
- Machining Execution: The CNC machine performs automated machining according to the programmed code.
CNC Setup
CNC setup is a crucial step in the machining process to ensure the machine, tools, workpiece, and program are in optimal condition for precise machining. The setup process includes initializing and resetting the machine, selecting and setting up tools, installing and positioning the workpiece, importing and verifying the machining program, and checking machine safety features. A test cut may be performed to verify and adjust parameters, ensuring the final part meets design specifications. The setup process ensures the machine operates efficiently and safely while maintaining accuracy and quality.
Advantages of CNC Machining
- High Precision and Repeatability: CNC machines offer extreme precision, often within microns, suitable for high-precision parts. They ensure consistent dimensions and shapes for each produced part, ideal for mass production.
- High Efficiency: Automated CNC machines run continuously, reducing manual intervention and increasing efficiency. Multi-axis CNC machines can complete multiple complex processes in one go, shortening production cycles.
- Flexibility and Adaptability: CNC machining can easily adapt to different parts by modifying programs, reducing machine setup time, and accommodating custom production needs.
- Reduced Human Error: CNC machines reduce the likelihood of human error compared to manual operations, enhancing quality and yield.
- Complex Shape Machining: CNC machining handles complex geometries, including curved and irregular shapes, which manual machines cannot achieve.
- Material Savings: Precise cutting reduces material waste, which is crucial for expensive materials, lowering production costs.
- High Automation: CNC machines can operate unattended, including overnight, increasing productivity and reducing labor costs.
- High Safety: Operators are shielded from cutting tools, minimizing safety risks. Machines often have safety features like protective doors and emergency stops.
- Scalability: CNC technology supports both small-batch and large-scale production, adapting to market demands and maintaining competitiveness.
- Data and Quality Management: CNC machines record processing parameters and operational data, aiding process control and quality management. Data analysis helps optimize production processes and improve product quality.