Surface Machining Capabilities of Five-Axis CNC Machines
Five-axis CNC (Computer Numerical Control) machines have revolutionized modern manufacturing by enabling the production of complex geometries with high precision. These machines are indispensable in industries such as aerospace, automotive, and medical device manufacturing, where intricate components are commonplace. However, ensuring the accuracy and reliability of five-axis CNC machines is paramount. This necessitates robust evaluation methods to assess their surface machining capabilities. This article explores recent advancements in test artifacts and measurement techniques designed to address these challenges, providing a more comprehensive assessment of five-axis CNC machine capabilities.
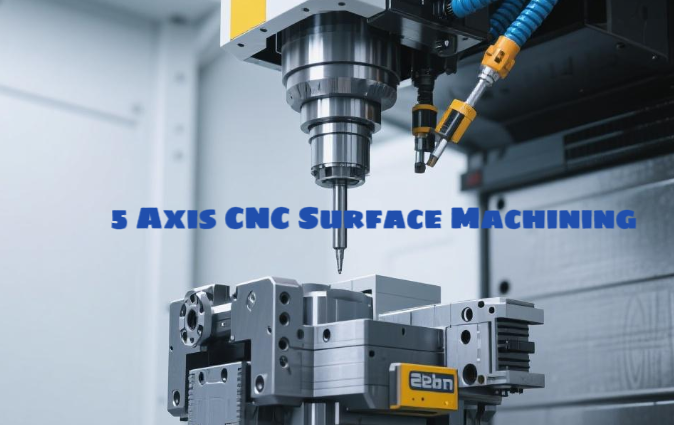
Traditional Evaluation Methods
Historically, the evaluation of five-axis CNC machines has relied on standardized test artifacts. One of the earliest and most widely recognized standards is the NAS979, developed by the National Aerospace Standard. This standard utilizes a cone frustum test piece to assess machine accuracy . While effective in certain aspects, such traditional methods often fall short in evaluating the dynamic performance and complex surface machining capabilities of modern five-axis machines.
Limitations of Existing Test Artifacts
The primary limitation of traditional test artifacts lies in their inability to replicate the complex geometries encountered in real-world applications. For instance, the NAS979 cone frustum primarily assesses geometric accuracy but does not adequately evaluate the machine’s performance in machining surfaces with varying curvature and continuity. Moreover, these artifacts often fail to isolate specific error sources, making it challenging to identify and rectify underlying issues .
Advancements in Test Artifacts: The “S” Shaped Test Piece
To address the shortcomings of traditional test artifacts, researchers have developed more sophisticated test pieces, such as the “S” shaped test artifact. This test piece is designed to evaluate the dynamic accuracy of five-axis CNC machines by incorporating complex surface geometries that mimic real-world components .
Design Features
The “S” shaped test piece consists of two primary surfaces:
- Surface A: Composed of arcs and straight lines, this surface exhibits constant curvature with varying continuity levels.
- Surface B: A cubic B-spline surface with continuously changing curvature, designed to assess the machine’s ability to handle dynamic changes in surface geometry.
These surfaces are strategically designed to evaluate the machine’s performance in machining areas with different curvature continuity, such as G1 (tangent continuity) and G2 (curvature continuity).
Evaluation Methodology
The evaluation of a five-axis CNC machine’s surface machining capabilities using the “S” shaped test piece involves several key steps:
1. Geometric Modeling
The test piece is modeled using CAD software, ensuring precise definitions of the complex surfaces and their respective curvature properties.
2. CAM Processing
Using Computer-Aided Manufacturing (CAM) software, the machining paths are generated. The process typically involves three stages:
- Roughing: Rapid material removal to approximate the final shape.
- Semi-Finishing: Refinement of the shape, leaving a small allowance for finishing.
- Finishing: Final machining to achieve the desired surface finish and dimensional accuracy.
3. Machining
The test piece is machined on the five-axis CNC machine under evaluation, following the generated tool paths.
4. Measurement and Analysis
Post-machining, the test piece is measured using a Coordinate Measuring Machine (CMM) to assess the surface accuracy. Measurements focus on key areas, particularly regions with curvature transitions, to evaluate the machine’s dynamic response.
Sample Measurement Data
The following table presents sample measurement data obtained from evaluating a five-axis CNC machine using the “S” shaped test piece:
Surface | Section | Curvature Continuity | Max Deviation (mm) | Mean Deviation (mm) | Standard Deviation (mm) |
---|---|---|---|---|---|
A | 1 | G1 | 0.045 | 0.020 | 0.012 |
A | 2 | G2 | 0.030 | 0.015 | 0.010 |
B | 1 | G1 | 0.050 | 0.025 | 0.015 |
B | 2 | G2 | 0.035 | 0.018 | 0.011 |
Note: The deviations are calculated based on the differences between the machined surface and the CAD model.
Interpretation of Results
The measurement data indicates that the machine exhibits higher deviations in areas with G1 continuity compared to G2 continuity. This suggests that the machine’s dynamic response to abrupt changes in curvature (as in G1 transitions) is less precise than its response to smoother transitions (G2). Such insights are crucial for applications requiring high surface accuracy, as they highlight potential areas for machine calibration or process optimization.
Advantages of the “S” Shaped Test Piece
The “S” shaped test piece offers several advantages over traditional test artifacts:
- Comprehensive Evaluation: By incorporating surfaces with varying curvature and continuity, it provides a more holistic assessment of the machine’s capabilities.
- Dynamic Performance Assessment: It evaluates the machine’s response to dynamic changes in surface geometry, which is critical for complex part manufacturing.
- Error Source Isolation: The design allows for the identification of specific error sources, facilitating targeted improvements.
Evaluating the surface machining capabilities of five-axis CNC machines is essential for ensuring the production of high-precision components. Traditional test artifacts, while useful, may not adequately assess the dynamic performance required in modern manufacturing. The “S” shaped test piece presents a more comprehensive and insightful evaluation method, enabling manufacturers to identify and address specific machine limitations.