Square Sheet Metal Mold: Process, Properties, Applications & Design Tips
For those who have never been exposed to the sheet metal industry, professional knowledge about sheet metal is definitely unfamiliar. When it comes to manufacturing square sheet metal molds, it is crucial to ensure that the design and manufacturing of the molds meet high quality standards. The square sheet metal mold not only requires precise shape control, but also needs to consider how to handle waste and ensure the stability of product shape during the stretching process. Today we will introduce the methods, advantages, applications, and optimization of mold clearance settings for square sheet metal molds.
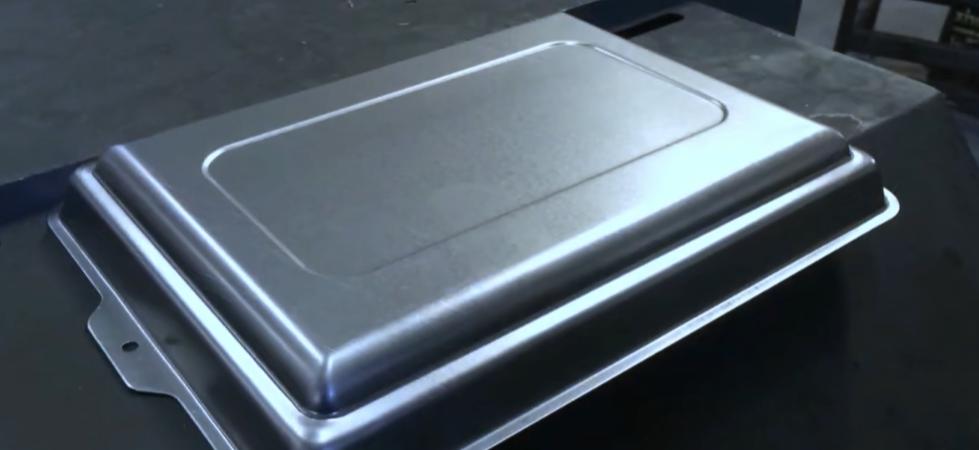
What is a Sheet Metal Mold?
Sheet metal mold is a type of mold used for metal forming, mainly used to process metal sheets or pipes into the desired shape and size of metal parts through cold stamping or hydraulic forming methods. The design and production of sheet metal molds need to be based on the shape and size requirements of the product to ensure accurate machining of the required shape.
The Manufacturing Process of Square Sheet Metal Molds
- Design the mold structure. Mainly design the shape and size of the upper and lower molds of the stretching mold, so that it can achieve the functional form of upward stretching of the sheet metal plate.
- Make stretching molds. The stretching mold adopts a simple upper and lower template structure to create the shape of two mold templates, and a floating plate is made on the lower mold.
- Select sheet metal material. Select sheet metal panels with appropriate specifications and thickness as production materials.
- The first step of production. Load the sheet metal plate between the upper and lower mold surfaces of the stretching mold, and use the stretching mold to stretch the sheet metal plate upwards to achieve a preliminary shape.
- Forming and shaping. Place the initially stretched sheet metal plate into the second shaping mold for secondary shaping, and perform external punching processing at the same time.
- Remove the product. Lift the finished product and waste material out of the mold through the floating plate of the lower mold, and remove the product and waste material separately.
- Batch production. Repeat steps 4-6 to achieve small batch production.
- Improvements and updates. Make necessary mold improvements and updates based on actual production conditions.
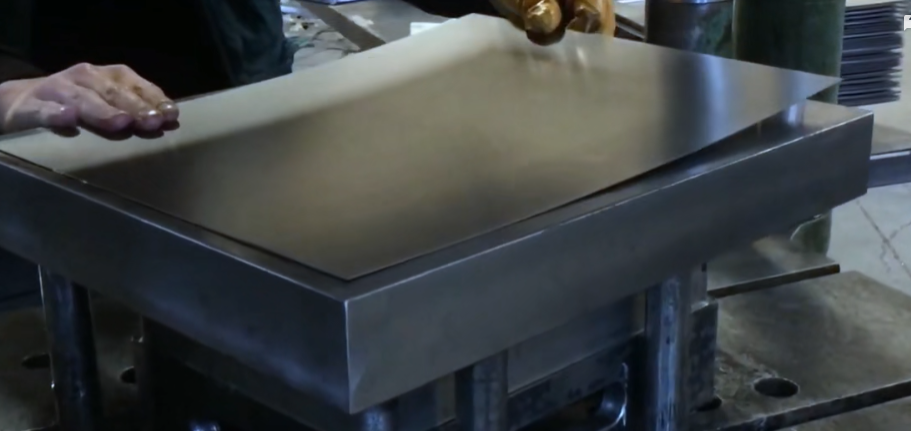
Advantages & Disadvantages of Square Sheet Metal Molds
Advantages:
Simple structure, only consisting of two templates, with low production and processing difficulty, and low cost. Using two templates for milling can achieve stretching forming, with a short production cycle and low processing costs.
The mold is easy to make and maintain, just milling two templates is enough. If there are problems during use, it is also easy to open the mold for repair and improvement. Unlike other molds with complex structures, the production cost and maintenance difficulty are high.
Suitable for small batch production, achieving stretching and forming according to this simple structure, suitable for some small batch production projects with low output but frequent changes in demand. For this application scenario, the cost-effectiveness is very high.
Disadvantages:
The waste treatment after stretching molding is complex, and it is difficult for the waste to detach from the mold edge after molding, requiring manual peeling and cutting. The cost and efficiency have relatively decreased.
The product form is difficult to precisely control, and relying solely on templates for stretching is difficult to ensure high precision in product form. The scope of application for some products that require high precision is limited to a certain extent.
Through the above analysis, we can see that although the square sheet metal stretching mold adopts a simple structure with low cost, its shortcomings in product accuracy and waste treatment are also quite obvious.
In Which Application Scenarios Are Square Sheet Metal Stretching Molds More Advantageous?
Square sheet metal stretching molds are widely used in small batch production. Although these simple structured stretching molds have certain defects in product shape precision control and waste disposal links, their advantages of low cost and simple structure make them very suitable for the production of small batch customized products.
For projects with small product quantities but frequent adjustments in drawing design, using such molds can quickly respond to market demand and produce new product samples and small batch products. At the same time, due to low investment, even if there is a change in the direction of product development in the later stage, there is basically no loss.
In addition, for the production of some simple specification products or prototype prototypes, using stretching molds is also more efficient. The shape can be seen by milling only two templates, which is very helpful for verifying the initial design.
Overall, although square sheet metal stretching molds do not require high precision, they have played a good role in small batch scenarios that require rapid product updates and validation of new ideas. Many enterprises use them for small batch trial production. Due to its low cost, it has the least impact on failure or even direction change, which is also the biggest advantage of the application.
So for industrial customized products with short production cycles and low output, stretching molds are the most widely used. It solves the molding needs of such projects with excellent cost-effectiveness.
Is There Any Other Method Besides The Upward Drawing Mold Structure When Making Square Molds?
Pull down structure: This structure is a steel pulling mechanism assembled under the surface of the mold, which forms the material through downward tension. Compared to upward stretching, it avoids uneven stretching areas inside the mold and stretches the material more evenly.
Diagonal drawing structure: Diagonal drawing structure utilizes inclined installation of steel pulling machinery to achieve material forming through oblique drawing. This structure provides a triangular stretching area with better stretching uniformity than upward stretching.
Multi point synchronous stretching structure: Multiple steel pulling points are evenly arranged around the mold, and the stretching force of different steel pulling points is controlled collaboratively to achieve synchronous forming of the overall material. This structure has more uniform stretching and good production efficiency.
Residual stress release structure: By adding a directional stretching module to the mold, the material can be stretched multiple times in different directions to achieve the goal of releasing residual stress. This can effectively improve the mechanical performance of the product.
Multi channel continuous stretching structure: using multiple small molds in series to continuously stretch elongated materials, saving process time and achieving efficient production. This is also one of the current hot research directions.
What is the difference between pull-down structure and upward stretching?
Simply put, the upward stretching structure involves stretching the material from bottom to top, but due to the larger stretching area at the bottom and smaller stretching area at the top, the uniformity of stretching is poor. The downward stretching structure is exactly the opposite, which uniformly stretches the entire material surface from top to bottom, using concentrated downward pulling force to achieve better stretching effect. Pulling down avoids the problem of large deformation in the lower part during upward stretching, and the stretching quality is more uniform. Therefore, it is suitable for forming thin plate materials with high stretching requirements.
How To Choose A Good Edge Cutting Tool After Drawing And Forming?
Edge cutting material: Select the appropriate edge cutting tool material based on the material to be cut. For steel, high-speed steel or ceramic blades are generally chosen; For non-metallic materials, carbonized hard alloys or polycrystalline Superhard can be considered.
Edge cutting depth: Select the size of the edge cutting depth according to product requirements, usually determined based on product drawings or samples.
Cut shape: Choose the cut shape, commonly including square, slanted mouth, and other different shapes.
Grinding tool type: Choose different types such as grinding rollers or grinding discs. Grinding rollers are suitable for surface edge cutting, while grinding discs are used for flat surface edge cutting.
Trimming thickness: Choose grinding tools with different thicknesses, and after rough grinding, fine grinding can improve efficiency and surface quality.
Processing parameters: Consider the feeding speed, wire feeding speed, and grinding tool speed, and set them reasonably according to the characteristics of the forming process.
Grinding tool matching: In complex forming surfaces, it is necessary to select a combination of grinding tools for synchronous forming processing.
Post processing: Choose whether to use post polishing or super polishing to remove burrs as needed.
Trial cutting and grinding: Conduct trial cutting and grinding before formal production, adjust parameters to avoid significant coordinate errors.
What Should We Pay Attention to When Trimming Products?
The most important thing in product edge cutting is to grasp the cutting parameters. We must reasonably determine parameters such as cutting speed, feed rate, and tool angle to ensure that the cut shape is neat, the surface is smooth, and there are no cracks or other defects. At the same time, passivation treatment of the incision is also very necessary, as it can eliminate residual stress at the incision, which is beneficial for improving the performance and safety of the product. In the process of edge cutting, the selection of cutting tools and cutting parameters is crucial. The following points should be noted:
Determine the working materials and their properties, and choose compatible tool materials, such as using high-speed steel knives for steel.
Consider the shape, size, and cutting depth of the product and choose a matching tool type, such as a ball knife or bag knife.
Pre cut and determine the rough parameters for the first cut, such as cutting speed and feed rate, appropriately.
Starting from rough cutting, gradually reduce the cutting depth and thickness, and optimize the cutting until it meets the requirements multiple times.
Pay attention to monitoring the morphology and surface quality of the incision, and adjust auxiliary conditions such as cutting angle and coolant flow rate if necessary.
It is best to conduct a metallographic test to detect the magnitude of residual stress and perform post-treatment.
Set the optimized cutting parameters for use in the CNC system.
Can The Cut Waste Be Reused?
According to the different types of materials, some materials have the same material as the main material for cutting edge waste, such as steel chips from steel cutting edges, which can be recycled and reused through melting and calcination. The edge cutting waste needs to be cleaned to remove impurities such as pollutants and grease, and then crushed using equipment such as a random mining machine to obtain smaller sized debris. The chemical composition and physical properties of the debris need to be tested to match the requirements of the raw materials before they can be reused. Repeated use should not be too frequent to avoid introducing impurities that may affect product quality. Generally not exceeding 3-5 times. Products with high requirements for surface thickness and surface smoothness are not recommended to use trimming waste.
How To Determine The Appropriate Value Of The Gap Between Square Sheet Metal Molds?
Firstly, we need to understand the design parameters of the product, including material, thickness, and dimensional changes. This is an important basis for determining the mold clearance in the future.
Then, we query the range of elongation for the material standard. For example, the tensile strength of commonly used steel is generally between 65% and 85%. The actual size change of the product, which is the size change value that needs to be stretched by the stretching mold, is called the theoretical stretching depth.
Based on this, we can calculate a certain proportion based on the stretching rate as a reference for the initial value gap. For example, for products that require a stretching depth of 5mm, we choose a parameter with a stretching rate of 65%, that is, the 65% of 5mm is 3.25mm, and take 3mm as the initial gap setting value.
Then, we need to develop experimental samples based on this gap value. The key here is to observe whether the actual stretching shape of the product at this gap matches the design requirements. If there is still a gap, we will fine tune the gap value based on the direction of the gap.
For example, if we find that the deformation is too large, we reduce the gap; If the deformation is insufficient, increase the gap value and then trial produce a new sample to observe the effect. It is necessary to repeatedly try and find the most stable gap parameter for the product shape.
Finally, considering certain tolerances in the actual production process, we need to leave a certain safety margin for the optimal clearance value to determine the final clearance specification for the mold. Simultaneously record the relationship between mold parameters and product materials and dimensions.