Annealing vs Normalizing: Differences in Cooling, Material Properties, Grain Size, Types, Cost
In metallurgy and material science, heat treatment processes like annealing and normalizing are essential for altering the physical and chemical properties of metals to enhance their workability. This guide explores these two processes, their process, purposes, applications, and differences.
What is Annealing?
Annealing is a heat treatment process used to alter the physical and sometimes chemical properties of a material. This process increases the material’s ductility and reduces its hardness, making it more workable.
- Purposes of Annealing
The primary purposes of annealing are to reduce the hardness of a material, relieve internal stresses, improve machinability, and facilitate further cold working by restoring ductility. This heat treatment process enhances the material’s toughness, making it more workable for subsequent shaping, stamping, or forming operations. Additionally, annealing helps redefine the grain size of the material, resulting in a more uniform and refined microstructure, which improves the overall mechanical properties and performance of the material under various working conditions.
- Process of Annealing
Heating: The material is heated above its recrystallization temperature.
Maintaining Temperature: The material is kept at this suitable temperature for a specified period.
Cooling: The material is then cooled down to room temperature. Cooling methods vary: Copper, Silver, Brass: Can be cooled slowly in air or quickly by quenching in water; Steel: Must be cooled slowly to anneal properly.
- Types & Applications of Annealing
Full Annealing: Heating steel to 30-50°C above its critical temperature and then cooling it slowly inside the furnace. Used for hot-worked sheets, forgings, and castings made from medium and high carbon steels.
Process Annealing: Heating steel to a temperature just below the lower critical temperature (723°C). Applied to cold-worked low carbon steel to reduce hardness and increase ductility.
Normalization: Heating ferrous alloys to 20-50°C above their upper critical point, soaking for a short period, and then cooling in air. Produces a uniform fine-grained structure, making the material tougher and more ductile. It eliminates columnar grains and dendritic segregation that can occur during casting.
What is Normalizing?
Normalizing is a heat treatment process used to make metals more ductile and tough after they have undergone thermal or mechanical hardening processes. This process is essential to restore the metal’s formability and machinability while reducing residual stresses.
- Purposes of Normalizing
The purpose of normalizing is to enhance the ductility and toughness of metals that have undergone thermal or mechanical hardening processes, which typically increase hardness but reduce workability. By heating the metal to an elevated temperature and then allowing it to cool in air, normalizing refines the grain structure, alleviates internal stresses, and produces a more uniform and homogeneous microstructure. This process makes the metal more formable and machinable while also reducing brittleness, ultimately improving its overall mechanical properties and performance in various applications.
- Process of Normalizing
Normalizing involves heating the metal to an elevated temperature and then allowing it to cool by exposing it to room temperature air. The process includes three main stages:
Recovery Stage: The metal’s temperature is raised using a furnace.
Recrystallization Stage: The metal is heated above its recrystallization temperature but below its melting temperature. New grains form without pre-existing stresses.
Grain Growth Stage: New grains fully develop.
- Applications of Normalizing
Normalizing is commonly used on: Alloy Steels and Carbon Steels. It is particularly useful after processes like cold rolling, which can increase brittleness due to work hardening.
Annealing vs Normalizing: Differences in Cooling, Material Properties, Grain Size, Types, Cost
Now let’s go over the differences between two heat treatment processes: annealing and normalizing:
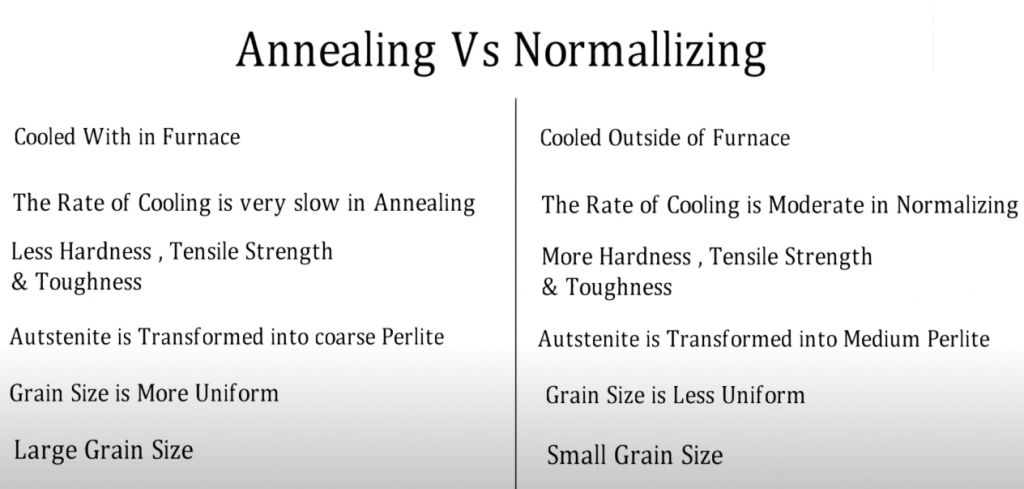
Cooling Method:
- Annealing: Cooling occurs slowly within the furnace.
- Normalizing: Cooling happens in air at room temperature, resulting in a faster cooling rate.
Cooling Rate:
- Annealing: The rate of cooling is very slow.
- Normalizing: The rate of cooling is moderate.
Mechanical Properties:
- Annealing: Coarse pearlite transformation. Less hardness, tensile strength, and toughness. More uniform grain size.
- Normalizing: Medium pearlite transformation. More hardness, tensile strength, and toughness. Less uniform grain size.
Grain Size:
- Annealing: Coarse grain size, Large grain size.
- Normalizing: Medium grain size, Small grain size.
Types:
- Annealing: Different types of annealing.
- Normalizing: No categories, only the normalizing process.
Cost:
- Annealing: Generally more expensive due to additional furnace time.
- Normalizing: Less expensive as it does not require extended furnace time.
Both annealing and normalizing play crucial roles in metallurgy, enhancing various properties of metals to suit different industrial applications. Understanding their differences and specific uses can help in selecting the appropriate heat treatment process for your needs.