Arch Bridges & Slag Inclusions in Mold Manufacturing: Which is Better for Product?
In mold manufacturing, “arch bridge” and “slag inclusion” are two different design methods. Arch bridges are commonly used to ensure the accuracy of closed grooves, especially for structures that require high-precision height dimensions. And “slag inclusion” is used in die casting molds to ensure that there is no cold insulation phenomenon in the product, and its volume is generally about 70% of the mold’s air volume.
The choice of method that is more suitable for product window placement depends on specific product requirements and design requirements. If the product requires high-precision height dimensions, using an “arch bridge” may be more appropriate, as this method can better control the accuracy of the closed groove. However, if the main purpose is to prevent cold shuts, then “slag inclusion” may be a better choice, as it can be set at the alloy closure to ensure that the product does not have cold shuts.
Therefore, the choice between “bridging” or “slag bag” should be determined based on the specific requirements of the product. If high-precision height dimensions are required, you can choose “arch bridge”; If it is necessary to prevent cold insulation, “slag inclusion” can be selected.
What Are the Specific Applications and Advantages of “Arch Bridge” Design in Mold Manufacturing?
- In mold manufacturing, the specific application and advantages of “arch bridge” design are mainly reflected in the following aspects:
- Large span capability: The design of arch bridges enables them to span large spaces, making them suitable for bridge construction that requires large spans. This characteristic enables arch bridges to be used in mold manufacturing for designing and manufacturing structural components that require large space.
- Local materials: The materials used for arch bridges usually include bricks, stones, concrete, and other materials with good compressive performance. These materials can be directly obtained on site, reducing transportation costs and time, thereby reducing the overall cost and complexity of the project.
- Good durability: The structural design of the arch bridge makes it have good durability, with lower maintenance and repair costs. This is an important advantage for long-term use and maintenance in mold manufacturing.
- Beautiful appearance: The curve of the arch bridge is rounded, dynamic, and has a beautiful shape. This beautiful appearance design can be used in mold manufacturing to enhance the visual effect and market competitiveness of products.
- Simple construction: The construction of the arch bridge is relatively simple, and the technology is easy to master. This makes the mold manufacturing process more efficient, reducing technical barriers and training costs.
- Economic advantage: Compared with steel bridges and reinforced beam bridges, arch bridges can save a lot of steel and cement. This economic advantage makes arch bridges more attractive in mold manufacturing, especially in cost sensitive application scenarios.
- Strong adaptability: Steel tube concrete arch bridges have a strong adaptability during construction, and can use various construction methods such as unsupported cable lifting and rotating construction. This flexibility enables arch bridge design to better cope with various complex construction environments in mold manufacturing.
The specific application and advantages of arch bridge design in mold manufacturing mainly include large crossing capacity, local materials, good durability, beautiful appearance, simple structure, obvious economic advantages, and strong adaptability.
What is the Role of “Slag Inclusion” in Die Casting Molds and Its Impact on Product Quality?
In die casting molds, slag ladles (also known as cold material wells) play a crucial role, and their impact on product quality is multifaceted.
– One of the main functions of the slag ladle is to accommodate the cold metal liquid that first enters the mold cavity, as well as the gas and oxide inclusions mixed in. If these impurities are not effectively removed, they will enter the interior of the product during the die-casting process, leading to a decrease in the mechanical properties and surface quality of the product, thereby affecting its service life. For example, in magnesium alloy die castings, impurities in the slag ladle can significantly reduce the quality of the product.
– The slag ladle also controls the flow state of the metal liquid filling together with the pouring system to prevent local eddy currents. This helps to improve the distribution of temperature field in the mold cavity and reduce defects such as flow marks and cold shuts in castings. By using and selecting slag ladles reasonably, product quality can be improved, production costs can be reduced, and the development of the die casting industry can be further promoted.
– In addition, the slag ladle also has good thermal isolation performance, which can reduce heat transfer, improve metal fluidity, increase mold life, and optimize process parameters. In some cases, the position of the slag ladle can also serve as the top rod position to prevent damage to the product.
– However, the design and use of slag bags also need to pay attention to some issues. For example, improper operation during slag removal from castings may cause edge chipping and affect the yield of the product. Therefore, it is very important to design and optimize the slag ladle structure reasonably.
The slag package plays a crucial role in die casting molds, not only effectively removing impurities and improving product quality, but also optimizing process parameters and extending mold life.
How to Choose to Use “Arch Bridge” or “Slag Inclusion” Based on Product Requirements in Mold Design?
- In mold design, the choice between using “arch bridge” or “slag inclusion” mainly depends on the specific requirements of the product and the exhaust requirements during the production process. We can infer the following points:
- Product draft and parting design: When designing molds, it is necessary to consider the direction of the product’s draft and the setting of the parting line. This step is crucial for deciding whether to use an arch bridge or slag inclusion. If the product structure is complex and requires a large amount of space to achieve smooth demolding, it may be inclined to use arch bridges to provide more space.
- The design of runners and gates: The design of runners and gates directly affects the flow path and speed of molten metal, which in turn affects the efficiency of gas discharge. Arch bridges are usually used in larger molds because they can provide more spacious space to accommodate runners and gates, thereby helping to better control metal flow and exhaust.
- Exhaust demand: During the die-casting process, the gas in the molten metal must be effectively discharged to avoid defects. Arch bridges, due to their structural characteristics, are more suitable for situations that require larger spaces to ensure sufficient gas discharge. In contrast, slag inclusion may be more suitable for smaller molds or situations where exhaust requirements are not particularly high.
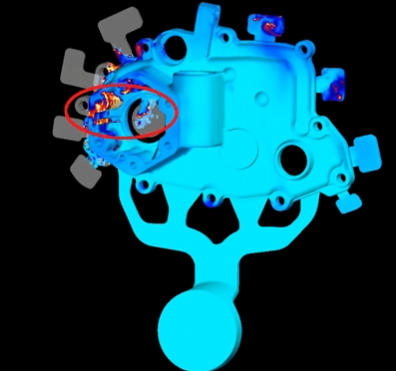
The choice of using “arch bridge” or “slag inclusion” in mold design should be based on the specific needs of the product, the size of the mold, and the requirements for exhaust efficiency.
What Other Design Methods Can Replace “Arch Bridges” or “Slag Inclusion” for Products With High Precision & High Dimensional Requirements?
- For products with high precision and high dimensional requirements, there are various design methods that can be replaced besides “arch bridge” or “slag inclusion”. Here are some feasible design methods:
- 3D printing technology: Through 3D printing technology, precise manufacturing of complex structures can be achieved. For example, the Striatus project utilizes 3D Concrete Printing (3DCP) technology to optimize the correlation between masonry structures and contemporary design, proposing a solution that can replace traditional concrete buildings.
- Precision manufacturing technology: Precision manufacturing technology includes using tools such as computer numerical control machines to manufacture high-precision and machinable components based on design. This method is widely used in the manufacturing of various high-precision products.
- Precision forming technology: Precision forming technology covers various technologies such as precision casting, precision forging, precision thermoplastic forming, precision welding and cutting. These technologies have been widely applied in the production of key components in products such as automobiles, washing machines, and household appliances.
- Ultra precision machining technology: Ultra precision machining technology includes ultra precision cutting, ultra precision grinding, ultra precision grinding and polishing technology, which can achieve surface accuracy at the nanometer or even sub nanometer level. This technology is suitable for products that require extremely high precision and surface quality.
- Digital manufacturing technology: By combining actual processes with intelligent sensors and software, manufacturers can improve processes, increase production efficiency and process capabilities. This method helps to achieve high-precision and high-quality production.
- Ultra high speed machining technology: Ultra high speed machining technology includes ultra high speed cutting and grinding mechanisms, ultra high speed spindle unit manufacturing technology, ultra high speed feed unit manufacturing technology, etc. This technology can complete high-precision machining tasks in an extremely short amount of time.
What Are Other Technologies or Methods to Prevent Cold Insulation in Mold Manufacturing?
Other techniques or methods to prevent cold insulation in mold manufacturing include the following:
- Increasing the pouring temperature of the metal liquid: By increasing the fluidity of the metal liquid, the occurrence of cold shut phenomenon can be reduced. However, it should be noted that the temperature should not be too high, otherwise it may cause gas to form bubbles in the metal liquid, affecting the quality of the die casting.
- Optimizing mold design: Reasonable mold design can effectively avoid cold insulation phenomenon. For example, adding risers, cold iron and other structures can improve the solidification conditions of aluminum alloy liquid and enhance the filling effect.
- Control mold temperature: For areas with larger wall thickness of the workpiece, the aluminum liquid solidifies slowly, and the mold temperature can be slightly lower; For rib plates, protrusions, or thin-walled areas, in order to prevent cold shuts, the fluidity of the aluminum liquid should be improved, and the mold temperature should be relatively increased.
- Improving the pouring speed and injection speed: By increasing the pouring speed and injection speed, the exhaust and filling conditions can be improved, the activity of the aluminum liquid can be increased, and the phenomenon of cold shuts can be reduced.
- Reasonably adjust the pouring system: Especially the number and distribution of the inner gates, ensure that the density of the pouring system is moderate, and standardize the pouring operation. Check the thermal expansion and contraction of the mold: Ensure that the mold temperature is close to the casting temperature to avoid cold insulation caused by excessive temperature differences.
- Improve mold manufacturing accuracy: Improve the machining and assembly accuracy of the mold, ensure the smoothness and dimensional accuracy of the mold cavity, and thus reduce cold shut phenomenon.