Best Custom CNC Fixtures – Top 10 Creative CNC Workholding Methods & Solutions
CNC machining requires precision, and a significant part of achieving that precision lies in effective workholding methods. Here we look at the most creative and efficient CNC fixture and workholding methods that have revolutionized CNC machining.
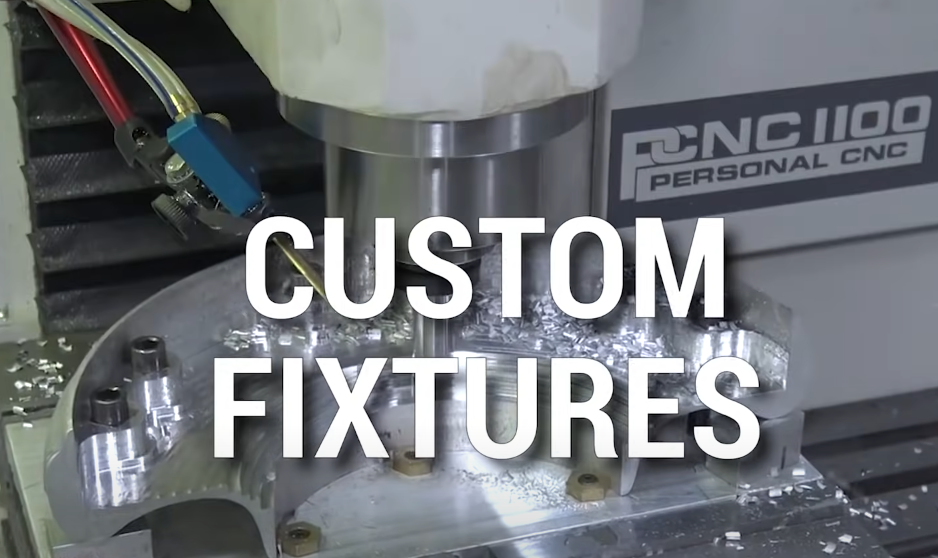
Top 10 Creative Custom CNC Workholding Fixtures & Clamps
Work holding is truly one of the most important aspects to learning CNC Machining or Manufacturing. In general, if you want to make a part faster, you’ve got to hold it with more rigidity; if you want to make it accurate, you got to make sure that your fixtures aren’t moving around or they’re not being affected by thermal influence by the heat and the cold. There are whole wide array of different options to hold on to different pieces of work, here we want to list the top 10 creative CNC workholding fixtures & clamps!
1. Traditional and Modified Vises
Vises remain one of the most commonly used methods for holding workpieces in CNC machining. A conventional machinist’s vise can be modified for CNC use by machining its edges flat, allowing it to be turned on its side, thereby increasing versatility. For specific projects, soft jaws
made from aluminum can be custom shaped to match the part being machined, increasing the holding capacity and precision.
2. Pearson Workholding System
The Pearson Pallet System stands out due to its versatility. It uses a combination of high spring pressure and accurately ground pads to secure fixtures onto the pallet, ensuring stable and precise workholding. This system is adaptable to various configurations, including magnetic and vacuum setups, making it suitable for thin or lightweight components.
3. Vacuum Fixtures
Vacuum holding systems are particularly beneficial for securing thin, non-magnetic materials like plastics or thin metals. By creating a powerful suction force, these systems hold the workpiece firmly in place without the need for physical clamps, minimizing potential damage and allowing full access to the workpiece’s surface.
4. Magnetic Chucks
Magnetic chucks are useful for holding ferromagnetic materials. They provide a strong, uniform holding force, which can be crucial when machining large or awkwardly shaped parts. The ability to quickly switch the magnetic force on and off helps in rapid setup changes and removal of the workpiece.
5. Chucks and Collets
Especially on lathes, chucks are indispensable. They can be used in mills as well by adapting them to fixture plates or directly mounting them to the machine table. Collets provide another option for holding cylindrical parts and can be particularly useful in multi-axis machining where access and clearance are priorities.
6. Custom Tombstones and Pallets
For batch production or multi-face machining, custom tombstones and pallets can be designed to hold multiple parts or provide multiple face access in a single setup. This method significantly reduces setup time and increases machining efficiency.
7. Modular Fixturing Systems
Systems like the M Lock workholding devices offer a modular approach, where parts can be moved and secured rapidly, making them ideal for multi-axis CNC machines. These systems often use dovetails and other interlocking mechanisms to ensure the workpiece remains secure during complex machining operations.
8. 3D Printed and Laser Cut Fixtures
With advancements in additive and subtractive manufacturing technologies, creating custom fixtures using 3D printers or laser cutters has become a viable option. These can be specifically designed to fit unique or complex shapes, providing precise location and support where traditional methods fall short.
9. Toe Clamps and Machinist Jacks
Toe clamps and machinist jacks offer simple yet effective solutions for securing workpieces directly to the machine table. They are particularly useful for irregular setups or when machining force needs to be distributed evenly across a fragile part.
10. Hybrid Techniques
Innovative combinations of these methods often yield the best results. For example, using a magnetic chuck in conjunction with custom soft jaws, or combining vacuum pads with modular pallet systems, can address complex workholding challenges effectively.
The world of CNC fixturing is vast and varied, and these top methods and solutions represent just a snapshot of the ingenious approaches used in modern machining. Each method has its strengths and is suited to particular types of jobs. The key to successful CNC machining lies in selecting the right workholding method for the job at hand, ensuring both efficiency and precision in your manufacturing processes.