Cast Aluminum vs Cast Iron: Differences in Properties, Processing, Uses, Cost
Cast aluminum and cast iron are common metal casting processes used to manufacture various mechanical parts, automotive components, and construction elements. This article will provide a detailed introduction to the processes of casting aluminum and iron, including their material composition, performance, processing techniques, applications, and price, and will summarize their differences.
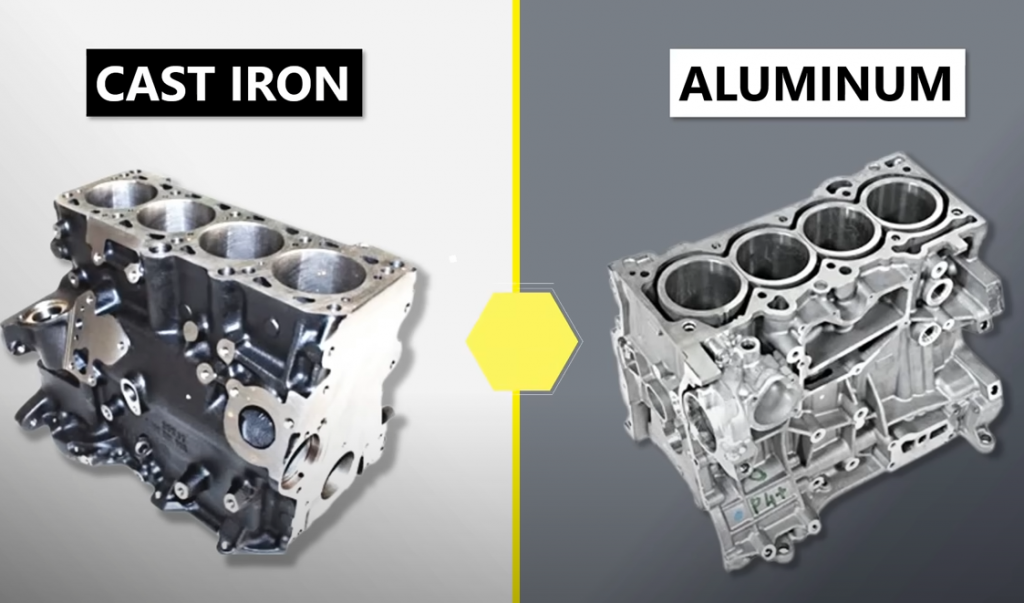
1. What is Cast Aluminum?
Cast aluminum is a process that involves melting pure aluminum or aluminum alloy ingots according to specific composition ratios, then pouring the molten material into molds, and cooling it to form the desired shape. The aluminum used in this process is known as cast aluminum alloy. Let’s start by understanding the composition of cast aluminum alloys.
Composition of Cast Aluminum Alloys
The composition of cast aluminum alloys varies depending on the alloy type and application requirements. Here are some major standards and recommended values:
- American Standard ASTM B85-98: Suitable for hot chamber and cold chamber die casting alloys including 360.0, 380.0, 413.0, C443.0, and 518.0.
- Japanese Standard: ENAC-43400 alloy, with chemical composition including Si 9.0%, Fe 11.0%, Cu 0.45%, Mn 0.9%, Mg 0.08%, Ni 0.55%, Zn 0.20%, Pb 0.15%, Sn 0.15%, Ti 0.05%.
- Chinese Foundry Association Standard TCFA 0203112—2020: Recommended chemical composition for aluminum alloys used in structural die casting.
- International Standard TTC: Specifies the chemical composition limits for various elements such as silicon, iron, copper, manganese, magnesium, chromium, zinc, and titanium.
- 6061 Aluminum Alloy: Composition range includes Si 0.40 – 0.80%, Fe ≤ 0.70%, Cu 0.15 – 0.40%, Mn 0.8 – 1.2%, Mg 0.8 – 1.2%, Cr ≤ 0.25%, Zn ≤ 0.25%, Ti ≤ 0.15%.
- A356 Aluminum Alloy: Composition includes Si 6.5 – 7.5%, Mg 0.20 – 0.40%, Fe ≤ 0.20%, Cu ≤ 0.20%, Mn ≤ 0.10%, Zn ≤ 0.10%.
With an understanding of the composition, let’s explore the advantages and disadvantages of cast aluminum.
Advantages and Disadvantages of Cast Aluminum
Advantages:
- High Strength and Toughness: Cast aluminum has good strength and toughness, especially certain high-strength casting aluminum alloys like ZL205A, which have high strength and good toughness.
- Thermal and Electrical Conductivity: Cast aluminum has good thermal and electrical conductivity, making it competitive in some special applications.
- Corrosion Resistance: Cast aluminum exhibits good corrosion resistance in atmospheric and seawater environments, suitable for applications requiring corrosion resistance.
- Good Machinability: Cast aluminum is easy to machine, facilitating various mechanical processing.
Disadvantages:
- Single Composition: Due to its relatively uniform composition, its strength may not be as high as some composite materials.
- Heavier Weight: The density of cast aluminum is higher than iron, making it heavier for the same volume, which can be a disadvantage in some applications.
Next, let’s delve into the processing steps of cast aluminum.
Cast Aluminum Processing Procedure
The processing of cast aluminum involves several critical steps:
- Mold Design: Design the mold based on the shape and size requirements of the part. Molds can be made of sand, metal, ceramic, etc., depending on the specific needs.
- Mold Preparation: Prepare the mold according to the design drawings and requirements. Typically, sand casting is used for cast aluminum, requiring the mixing of sand materials (like quartz sand, gypsum sand) with binders and filling the mixture into molds, followed by vibration compaction.
- Molten Metal Treatment: Treat the molten aluminum according to the desired properties of the casting. This usually involves melting, purification, and alloying steps to ensure the casting has good mechanical and physical properties.
- Casting Operation: Place the mold in the casting equipment, preheat it, and pour the molten aluminum. The aluminum fills the mold cavity to form the shape of the casting.
- Cooling Treatment: After casting, allow the surface of the casting to solidify before removing it from the mold. The casting then needs to cool gradually to ensure uniform and complete formation of the internal metal structure.
- Sand Removal and Cleaning: Remove the cooled casting from the mold and use mechanical or chemical methods to remove sand particles from the surface and interior.
- Finishing and Machining: Process the casting to meet precision, surface quality, and assembly dimensions, sometimes requiring heat treatment to enhance properties.
- Surface Treatment: Improve the appearance and prevent corrosion through grinding, polishing, spraying, etc.
- Inspection and Quality Control: Inspect the cast aluminum part for appearance, dimensions, mechanical properties, etc., to ensure it meets design requirements and maintain quality control.
Having understood the processing steps, let’s look at the applications of cast aluminum.
Applications of Cast Aluminum
Cast aluminum is widely used in automotive components, construction elements, and various mechanical parts, such as cylinder blocks, gearboxes, engine mounting brackets, and escalator steps.
Next, let’s shift our focus to another important material—cast iron.
2. What is Cast Iron?
Cast iron is an iron-carbon alloy with a carbon content greater than 2.1%. Its main components include iron, carbon, and silicon, with additional alloying elements such as manganese and phosphorus to enhance performance. Compared to pig iron, cast iron has a higher carbon content and different casting properties. Let’s examine the composition of cast iron.
Composition of Cast Iron Alloys
The composition of cast iron typically includes:
- Carbon (C): 2.5% to 4.0%
- Silicon (Si): 0.6% to 3.0%
- Manganese (Mn): 0.2% to 1.2%
- Phosphorus (P): 0.04% to 1.2%
- Sulfur (S): 0.04% to 0.20%
Additionally, cast iron may contain other alloying elements such as nickel, chromium, molybdenum, aluminum, copper, boron, and vanadium, depending on the type and use of the cast iron. For example, ductile iron may include small amounts of nickel and copper to improve mechanical properties and wear resistance.
Having understood the composition, let’s discuss the advantages and disadvantages of cast iron.
Advantages and Disadvantages of Cast Iron
Advantages:
- Good Castability: With a low melting point (about 1200℃) and good fluidity, cast iron can be cast into complex shapes.
- High Wear Resistance: The presence of graphite gives cast iron good wear resistance, making it suitable for applications requiring high hardness and severe wear conditions.
- Good Vibration Damping: Cast iron has good vibration damping properties, making it widely used in mechanical manufacturing, such as for machine tool beds and spindle boxes.
- Low Notch Sensitivity: Cast iron has no distinct yield stage during fracture, resulting in low notch sensitivity, which helps improve crack resistance.
- Good Machinability: Due to the presence of graphite, cast iron is easier to machine than steel.
- Low Cost: The production cost of cast iron is relatively low, making it an economical choice for many applications.
Disadvantages:
- Poor Mechanical Properties: Although cast iron has the above advantages, its mechanical properties (such as strength, plasticity, and toughness) are generally inferior to steel. Gray cast iron, in particular, has significantly lower tensile strength, plasticity, and toughness than carbon steel.
- High Brittleness: Due to the presence of graphite, cast iron tends to be brittle and can fracture easily, especially under rapid cooling.
- Poor Weldability: Cast iron is difficult to weld and prone to cracking and white iron formation during welding, limiting its use in applications requiring welding.
- Limited Heat Treatment: The heat treatment effect of gray cast iron is limited, and rapid cooling heat treatment methods are difficult to implement.
- Non-uniform Structure: The structure of cast iron can be non-uniform, leading to variability in overall performance, especially with differences in properties at various locations.
Next, let’s delve into the processing steps of cast iron.
Cast Iron Processing Procedure
The processing of cast iron involves several critical steps:
- Mold Design: Design the mold based on the shape and size requirements of the part. Typically, sand casting is used for cast iron, requiring the design of appropriate mold textures, gating systems, and cooling systems.
- Mold Preparation: Prepare the mold according to the design drawings and requirements. Generally, the preparation of sand molds for cast iron is complex, requiring the preparation of patterns, then mixing sand materials (such as quartz sand, gypsum sand) with binders, and filling them into the molds, followed by vibration compaction.
- Molten Metal Treatment: Treat the molten iron to improve the performance and quality of the casting. Common treatments include melting, degassing, and alloying.
- Casting Operation: Place the mold in the casting equipment, preheat it, and pour the molten iron. The iron fills the mold cavity to form the shape of the casting.
- Cooling Treatment: After casting, allow the surface of the casting to solidify before removing it from the mold. The casting then needs to cool gradually to ensure uniform and complete formation of the internal metal structure.
- Sand Removal and Cleaning: Remove the cooled casting from the mold and use mechanical or chemical methods to remove sand particles from the surface and interior.
- Finishing and Machining: Process the casting to meet precision, surface quality, and assembly dimensions, sometimes requiring heat treatment to enhance properties.
- Heat Treatment: Some cast iron parts need heat treatment to improve their mechanical and physical properties. Common heat treatment methods include annealing, normalizing, and quenching.
- Inspection and Quality Control: Inspect the cast iron part for appearance, dimensions, mechanical properties, etc., to ensure it meets design requirements and maintain quality control.
Having understood the processing steps, let’s look at the applications of cast iron.
Applications of Cast Iron
Cast iron is widely used in mechanical manufacturing, automotive manufacturing, and railway engineering, such as crankshafts, camshafts, brake discs, oil pump housings, manhole covers, etc.
Understanding the characteristics of both cast aluminum and cast iron, let’s compare them to better understand their differences.
3. Differences Between Cast Aluminum and Cast Iron
Cast aluminum and cast iron differ significantly in terms of performance, machinability, and cost. Let’s compare these aspects in detail.
Performance
Due to their different material compositions, cast aluminum and cast iron have distinct performance characteristics. Cast aluminum has better strength and toughness, making it suitable for applications requiring high strength and toughness. Cast iron, on the other hand, has higher strength and hardness, making it suitable for mechanical components that need to withstand high loads.
Strength
The material composition affects the strength and hardness of the cast materials. Cast iron has higher strength and hardness, making it suitable for mechanical parts that need to withstand high loads. Cast aluminum, with its lower strength and hardness but better elasticity, is suitable for parts that require high density and thin-wall structures.
Weight
Cast aluminum has a lower density, making aluminum parts lighter than iron parts of the same size. This makes cast aluminum more suitable for applications requiring weight reduction, such as automotive manufacturing.
Machinability
Cast aluminum is easier to machine because it is a softer material, while cast iron, being very hard and brittle, is more challenging to machine and often requires special tools and methods.
Corrosion Resistance
The material composition of cast aluminum provides better corrosion resistance, allowing it to resist most chemicals and oxides. Cast iron, however, is prone to rust and corrosion, making it susceptible to cracking and breaking in humid and corrosive environments.
Cost
Cast iron has a lower production cost, making it more economical for various applications, while cast aluminum tends to have a higher cost.
To summarize the differences more clearly, let’s use a comparison table.
Summary Table
Property | Cast Aluminum | Cast Iron |
---|---|---|
Strength | Good | High |
Toughness | Excellent | Poor |
Machinability | Easy to machine | Difficult to machine |
Corrosion Resistance | Excellent | Prone to rust |
Production Cost | Higher | Lower |
Applications | Automotive parts, construction elements, etc. | Mechanical manufacturing, automotive manufacturing, railway engineering, etc. |
Finally, let’s discuss the advantages of cast iron and cast aluminum in engine block applications.
4. Cast Iron or Cast Aluminum: Which is Best for Engine Blocks?
In the choice of engine blocks, both cast iron and cast aluminum have their advantages and disadvantages. Cast iron is traditionally used in automotive engines due to its high strength and wear resistance. However, cast aluminum, with its lightweight and excellent heat dissipation, is increasingly favored in modern high-performance and fuel-efficient engines. The specific choice depends on the design requirements and application scenarios of the engine.
Cast aluminum and cast iron each have their strengths and limitations in different applications. Choosing the right material requires a comprehensive consideration of performance, machinability, cost, and application requirements. We hope this article helps you better understand these two materials and make informed decisions in practical applications.