CNC Small Holes Drilling Guide (Tools, Runout, Feeds & Speeds)
Drilling extremely small holes with precision is no easy task, especially when working with carbide micro-drills. In this guide, we’ll walk through the process of using the Tormach 1100 MX and discuss the tools, techniques, and troubleshooting tips for achieving great results. From selecting the right drills to managing runout and optimizing feeds and speeds, this article will cover key considerations to ensure success.
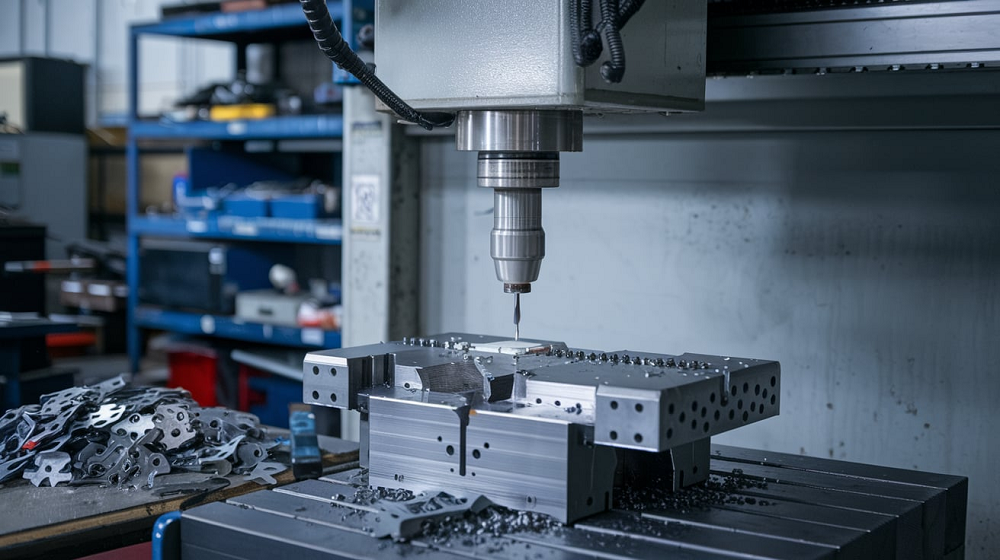
Tools Overview for Small Hole Drilling
To start, let’s discuss the three primary tools used in this process:
- Harvey Tool #20157
- Diameter: 0.0157 inches (approximately 1/64″)
- Length of Cut: 0.270 inches
- Helix Angle: 40 degrees
- Shank: Reduced shank with a 1/8″ diameter
- Lakeshore Carbide 1/32″ Split Point Drill
- Diameter: 1/32″ (twice the size of the Harvey Tool drill)
- Helix Angle: 15 degrees
- Shank: Straight
- Lakeshore Carbide Center Drill
- Used for spotting the holes before drilling.
Key Factors: Runout and Tool Holding
One of the most important considerations when working with small drills is runout—the wobble or deviation of the tool as it rotates. Excessive runout can quickly lead to tool breakage, especially with carbide drills, which are extremely rigid but brittle.
- The Harvey Tool, with its 1/8″ reduced shank, made it easier to find a collet for a firm grip, and the larger shank provided more material for making adjustments to reduce runout.
- The Lakeshore Carbide Drill, with its smaller straight shank, was much harder to secure properly, leading to more frequent tool failures.
Tip: Using small drills with a standardized larger shank (like 1/8″) can make them more versatile and easier to adjust for runout. This added flexibility helps when changing drill sizes or tweaking setups.
Drilling Techniques and Feeds/Speeds
Spotting the Holes
Before drilling, it’s essential to spot the holes using a center drill. Spotting to a depth of 0.002 inches was sufficient to guide the Harvey Tool drill, ensuring a straight start every time.
Using the Harvey Tool Drill
For the Harvey Tool 0.0157″ drill, the following parameters worked well:
- RPM: 10,000
- Surface Feet per Minute (SFM): 40
- Plunge Feed Rate: 4.5 inches per minute
- Feed per Revolution (FPR): 0.00045 inches
- Pecking Depth: 1x the drill diameter
In the first test, using the manufacturer’s recommended pecking depth (3x the diameter) resulted in rapid tool breakage. Adjusting to a smaller pecking depth significantly improved the outcome, allowing for a depth of up to 0.25 inches.
Using the Lakeshore Carbide Drill
For the larger 1/32″ drill, the process required more fine-tuning:
- Spotting Depth: 0.005 inches
- RPM: 10,000
- SFM: 81
- Plunge Feed Rate: 10 inches per minute
- FPR: 0.001 inches
- Pecking Depth: Approximately the diameter of the drill (0.037 inches)
A key finding was the importance of coolant. Running the drill dry resulted in immediate breakage, even at reduced feeds and speeds. Properly aimed coolant was necessary to keep the tool cool and operational.
Lessons Learned and Recommendations
- Runout Mitigation:
Investing in drills with larger, standardized shanks (e.g., 1/8″) simplifies tool holding and runout adjustments. While dedicated small-diameter shank drills may save money, they can be harder to manage in terms of setup precision. - Spotting:
Spotting the holes with a center drill is a must for small carbide tools. A shallow spot is enough to guide the drill and prevent deflection. - Coolant:
Small carbide drills cannot be run dry. A well-aimed coolant stream is vital for tool longevity and performance. - Pecking Depth:
Reducing pecking depth to around 1x the drill diameter proved to be more effective than the manufacturer’s recommended settings, especially for fragile micro-drills. - Feeds and Speeds:
Slower plunge feed rates and smaller feed per revolution settings significantly improve results. Experimentation is necessary to find the “sweet spot” for each tool.
Drilling small holes with carbide micro-drills requires attention to detail, from tool selection to proper setup and machining parameters. By focusing on factors like runout, spotting, coolant, and optimized feeds and speeds, you can achieve precise, repeatable results. While the process involves trial and error, the lessons learned along the way will make each cut more reliable and efficient.