Forming Tap vs Spiral Tap, Which is Better
As an important cutting tool, the correct application of taps can greatly enhance production efficiency. In various industrial fields, two common types of taps—forming taps and spiral taps—are widely used. Due to differences in their design structures, they are suitable for different processes and materials, each offering unique advantages. This article will comprehensively introduce the differences between forming taps and spiral taps.
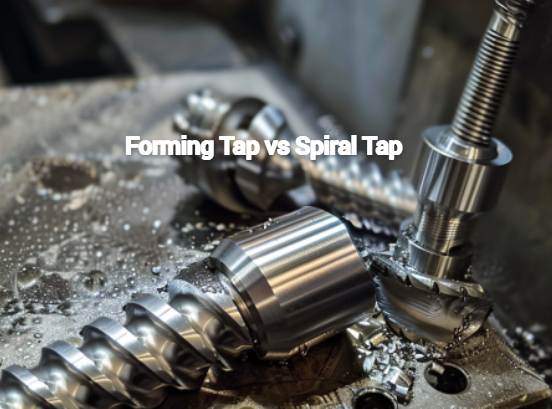
What is a Forming Tap?
A forming tap is a specially designed threading tool. It features a tapered structure from the head to the tail, with the thread pitch gradually increasing from the smallest at the head to the largest at the tail. This design, with threads going from fine to coarse, allows it to perform effectively at different stages of the drilling process, ensuring a smooth and seamless connection throughout. This makes it highly efficient for drilling in soft materials. For drilling in soft plastics, rubber, and similar materials, a forming tap is the best choice. In summary, a forming tap is a “stepped” threading tool with threads that go from fine to coarse, specifically designed for soft materials to provide efficient and stable drilling.
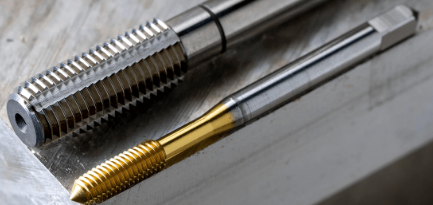
What is a Spiral Tap?
A spiral tap is an important type of tap. It has an overall conical shape with evenly distributed threads. This design offers significant advantages: the closely spaced, uniform threads enable efficient cutting of materials, with a high cutting volume per unit of time. Each thread bears a smaller cutting force, which reduces the risk of thread breakage at high speeds. Additionally, the rapid cutting speed of spiral taps makes them particularly suitable for tasks that require quick initial drilling. In summary, a spiral tap, with its highly uniform and dense thread structure, provides efficient and fast cutting capabilities.
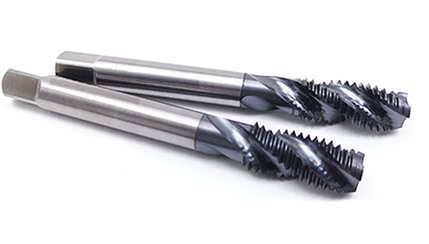
Differences between Forming Taps and Spiral Taps
Forming taps and spiral taps are two common types of taps, and they differ mainly in design and application:
1. Structure
Forming Tap: Tapered design from head to tail, with thread pitch increasing from fine to coarse.
Spiral Tap: Overall conical shape with uniformly distributed threads.
2.Thread Pitch
Forming Tap: The thread pitch is smallest at the head and largest at the tail, with a continuous variation.
Spiral Tap: The thread pitch is uniform and consistent throughout.
3. Suitable Materials
Forming Tap: Suitable for soft materials such as plastic and rubber.
Spiral Tap: Suitable for medium to hard materials like wood and non-metal materials.
4. Application Scenarios
Forming Tap: Used for drilling and advancing in soft materials.
Spiral Tap: Used for initial drilling tasks that require quick cutting.
5. Work Efficiency
Forming Tap: Smooth advancement from fine to coarse threads.
Spiral Tap: Higher cutting efficiency due to uniform thread pitch.
Appropriate Scenarios for Using Forming Taps and Spiral Taps
Based on their design and functions, the following scenarios are more suitable for their use:
1. Drilling in Soft Plastic or Rubber Materials: These soft materials are easily compressed, and the fine-to-coarse structure of forming taps can advance the drill evenly without damaging the material.
2. Multi-level Advancement Materials: For structures like plastic-metal composites, forming taps can control depth in layers.
3. Aesthetic Work Areas: Forming taps advance smoothly and regularly, ensuring a neat hole in plastic products.
4. Initial Drilling: For harder materials like wood and non-metals, spiral taps are quick and efficient.
5. Deep Cutting Tasks: For tasks like boring and through holes in plastic sheets, spiral taps offer robust support and high efficiency.
6. Mass Production: Due to their high efficiency, spiral taps are suitable for repetitive mass production tasks.
Industrial Applications of Forming Taps and Spiral Taps
Based on their design features, forming taps and spiral taps are widely used in the following industrial fields:
-Plastic Products Industry: Suitable for drilling in soft plastics and for creating through holes in plastic sheets.
-Electrical and Electronics Industry: Used in complex PCB board hole positions, with forming taps producing precise printed circuits.
-Home Furnishing and Building Materials Industry: Widely used for initial drilling in wooden furniture and softwood processing.
-Stone Industry: Used for engraving on natural and artificial stone surfaces.
-Hardware Casting Industry: Suitable for creating dense holes on aluminum alloy products.
Automotive Industry: Used for processing lightweight parts requiring various embedded structures.
-Communication Industry: Frequently used for dense screw holes in electronic circuit boards or plastic parts.
Advantages of Forming Taps and Spiral Taps in Soft and Hard Material Processing
For soft materials (such as plastic and rubber), the fine-to-coarse tapered structure of forming taps allows each segment of the thread to progressively release its cutting ability, ensuring smooth advancement without gaps. This is particularly suitable for delicate surface processing of soft materials. The fine threads at the head minimize damage to the soft material, providing an overall smooth drilling effect.
For hard materials (such as wood and non-metals), the uniform and dense threads of spiral taps enable each thread to participate in quick cutting, making initial drilling highly efficient. The tight structure also facilitates quick chip removal, preventing resistance. This is especially suitable for high-efficiency initial through-hole tasks, where the robust support structure is advantageous for use in harder materials.