GD&T Coaxial Controls: Symbols, Comparison, and Applications
Geometric Dimensioning and Tolerancing (GD&T) is a critical tool for ensuring the functionality and manufacturability of parts. Among the most common symbols used to control coaxiality in GD&T drawings are position and profile. In this blog, we will explore the differences between these two symbols, their applications, and how to choose the appropriate control for various cylindrical features. Using examples from Scott Neumann’s GeoTol Fundamentals and Advanced Programs, we’ll dive into practical insights and examples, including a rotating shaft assembly.
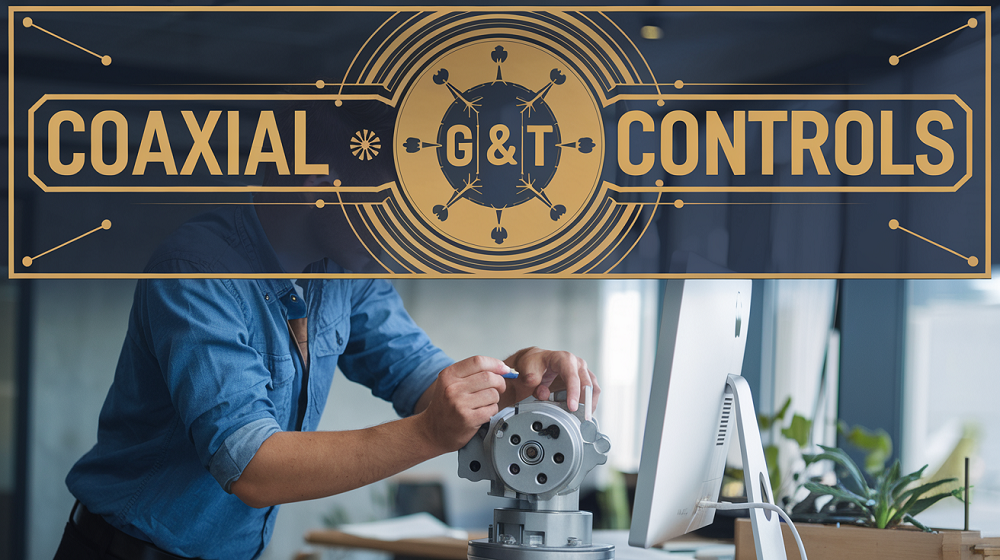
Position vs. Profile: What are the Differences?
Before diving into specific applications, let’s summarize the core differences between position and profile controls:
- Position Tolerance: Position tolerance creates a cylindrical tolerance zone, such as a diameter of 0.3, within which the axis of a feature must lie. This tolerance ensures the axis remains constrained to the specified zone, thus controlling its alignment and placement. To apply position tolerance, a size tolerance for the feature is also required, as it governs the size and form of the feature in accordance with Rule #1 of ASME Y14.5. Position tolerance primarily focuses on controlling the orientation, coaxiality, and location of the axis, making it an essential tool for ensuring proper alignment and functionality in designs where these factors are critical.
- Profile Tolerance: Profile tolerance directly controls the surface of a feature, ensuring its geometry adheres to specific requirements. It relies on basic dimensions to define the nominal geometry, while the profile tolerance simultaneously regulates size, form, orientation, and location. This comprehensive control makes profile tolerance ideal for features where all aspects of the geometry require consistent precision, such as seals or surfaces with critical fits. By addressing multiple factors in one tolerance, profile tolerance provides an efficient and effective solution for maintaining functional and manufacturing integrity.
The choice between these two symbols depends on whether you want separate controls for size and coaxiality (position) or a single control for all geometric aspects (profile).
Practical Application: Rotating Shaft Example
To better understand how position and profile tolerances are applied, let’s consider a typical rotating shaft example. This is a real-world case taken from Scott Neumann’s GeoTol Applications and Tolerance Stacks program, which is also discussed on page 15.2 in his book.
Defining the Datum Features
In GD&T, selecting the correct datum features is crucial for controlling a part’s functionality. For our shaft example:
- Datum A: The larger diameter of the shaft, which serves as the primary datum axis.
- Datum B: The smaller bearing journal. Together, Datum A and Datum B create a robust A-B datum axis, ensuring the shaft’s coaxiality.
- Datum C: The bottom shoulder where the main bearing seats, controlling the shaft’s orientation in the up-down direction.
By combining Datum A, B, and C, we establish a strong reference system to control all features relative to the bearings.
Diameter-by-Diameter Analysis
Now, let’s analyze each diameter on the shaft and determine whether to apply a position or profile tolerance:
- Coupling Diameter: The coupling diameter is a feature that fits into a coupling and requires a tight size tolerance to ensure an accurate fit. Since the coupling is flexible, coaxiality is less critical in this case. As a result, a position tolerance is applied to control the axis of the feature, ensuring proper alignment without over-constraining the design.
- Threaded Featur: The threaded feature is controlled by a thread specification, which ensures the thread fits properly. To maintain the thread’s alignment and prevent miscentering, a position tolerance is applied, keeping the feature centered and functional.
- Bearing Journal: The bearing journal demands a tight size tolerance to ensure a proper fit with the bearing. In addition to size, coaxiality is critical for the bearing’s performance. Therefore, both a size tolerance and a position tolerance are applied to control the fit and ensure precise alignment of the axis.
- Clearance Diameter: The clearance diameter is designed to provide clearance without requiring a tight fit. For this feature, a profile tolerance is suitable, as it controls both size and coaxiality in a single tolerance, offering a simple yet effective solution for geometric control.
- Seal Diameter: The seal diameter is critical for dynamic seals, where both size and coaxiality directly affect performance. A profile tolerance is applied to this feature to ensure consistent control of size, form, orientation, and location. This prevents uneven loading on the seal and ensures proper functionality over its lifespan.
- Propeller Mount Diameter: The propeller mount diameter is a feature that fits into the propeller. To ensure the propeller mounts securely, a size tolerance is applied to control the fit. Additionally, a position tolerance is used to control the alignment of the axis, minimizing potential vibration issues during operation.
Choosing Between Position and Profile
To summarize the decision-making process:
- Position Tolerance:Use when a feature must fit into something with a tight size tolerance, and coaxiality is a separate concern. Example: Coupling diameters, threaded features, and tight-fitting bearing journals.
- Profile Tolerance:Use when size, form, orientation, and location are equally important. Example: Seal diameters and clearance features.
Key Considerations for Profile Tolerances
When applying a profile tolerance, it’s essential to understand how it controls the feature:
- A profile tolerance creates a total tolerance zone. For example, a profile within 0.020 creates a ±0.010 zone around the nominal geometry.
- On cylindrical features, the profile tolerance applies all around the surface, controlling both size and coaxiality simultaneously.
- Be cautious when interpreting profile tolerances, as they can appear more lenient than they actually are.
Position and Profile: The GD&T Power Duo
For cylindrical features, position and profile are the two most commonly used symbols in GD&T. While runout is occasionally used for specific applications (e.g., pulleys or seal diameters), position and profile remain the go-to tools for controlling tolerances on shafts and round parts.
- Position: Ideal for controlling axis alignment in conjunction with a size tolerance.
- Profile: Perfect for controlling everything (size, form, orientation, location) in one step.
Choosing the right GD&T symbol—position or profile—depends on the functional requirements of your design. If the feature involves a tight fit, position tolerance with a separate size tolerance is often the best choice. For features like seals, where size and coaxiality are equally important, profile tolerance offers a comprehensive solution.
By understanding the strengths of these symbols and using practical examples, you can confidently apply GD&T to ensure both manufacturability and functionality. For more in-depth applications and examples, check out Scott Neumann’s GeoTol Fundamentals and Applications and Tolerance Stacks programs.