How to Heat Treat 45 Steel & 40 Cr Steel
For CNC machine tools, components like spindles, RAM, slides, etc. require a balanced combination of strength, rigidity, fatigue resistance, and machinability. 45 steel and 40Cr steel are often used due to their good machinability and ability to be processed via heat treatment to achieve the desired characteristics.
Some key heat treatment requirements and goals for CNC machine tool components include:
– Surface hardness of 50-58 HRC for wear resistance while maintaining core toughness.
– Compressive residual stresses in the surface and minimum risk of cracking.
– Fine and uniform prior-austenite grain size for consistent properties.
– Sufficient core toughness to withstand impacts and shock loads during machining operations.
– Dimensional stability at operating temperatures of machine tools.
– Corrosion and chemical resistance in aggressive coolant environments.
– Optimized strength-toughness balance as per the component design and loading conditions.
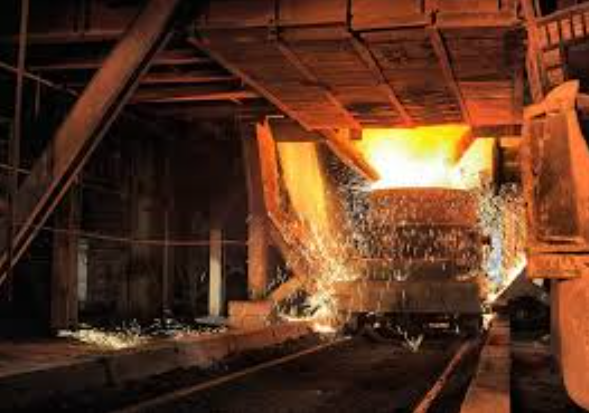
The standard heat treatment techniques used are normalized and tempered for 45 steel components, and induction hardening for 40Cr steel components to meet the above requirements. Modern heat treatment with advanced controls and monitoring ensures repeatable thermal processing to produce CNC machine tool components with highly consistent quality.
To summarize, heat treatment is a critical process to develop the required mechanical and functional properties in 45 steel and 40Cr steel used widely in the CNC machine tool industry. Proper selection of steel grade, optimal heat treatment parameters, and quality controls help achieve long-lasting and high-precision CNC machine tools.
For more information on CNC machine tools, please check https://cncguides.com/. CNCguides is a premier resource for guidance on CNC machines, manufacturing, and related topics. It provides comprehensive guides, tutorials, tips, and machine selection support for technologists, engineers, and shop-floor operators in the industry.
Material | Components requiring surface hardness like cutters, and drilling fixtures – able to be induction hardened | 40Cr Steel |
Chemical Composition | C: 0.4-0.5%, Mn: 0.3-0.8%, Si: 0.15-0.3%, Cr: 4.75-5.5%, Ni: 1.65-2.15%, Mo: 0.2-0.3% | C: 0.38-0.43%, Cr: 3.5-4.5%, Mo: 0.15-0.3%, V: 0.15-0.3% |
Hardness After Heat Treatment | HRC 55-58 (hardened and tempered) | HRC 58 (induction hardened case), HRC 45 (core) |
Tensile Strength | 1300-1500 MPa (hardened and tempered) | 1400 MPa (induction hardened case), 1000 MPa (core) |
Impact Toughness | 15-25 J (hardened and tempered) | 15 J (hardened case), 40 J (core) |
Dimensional Stability | Good | Excellent |
Wear Resistance | Good | Excellent |
Machinability | Excellent | Good |
Applications in CNC Machines | Spindles, ram, slides – requiring good strength and fatigue resistance | Components requiring surface hardness like cutters, and drilling fixtures – able to be induction-hardened |
45 Steel Components
– Machine spindle: requires high strength, rigidity, and fatigue life.
– Ram/cross-slide: transfers motion accurately with minimal deflection.
– Work table: provides a sturdy and stiff base for machining operations.
– Guideways: precisely locates and supports moving components.
– Ball screws: transmits rotational motion to linear motion accuracy.
– Cast iron housings: provide a robust framework for components.
40Cr Steel Components
– Milling cutters: demands high surface hardness for tooth integrity.
– Drill bits: need wear resistance to puncture tough materials.
– Broaches: the surface must resist abrasion during shaping.
– Toolholders: inductively hardened outer surface grips cutters firmly.
– Work fixtures: accurately locates parts under clamping forces.
– Jaws/chucks: securely hold pieces without galling or disruption.
– Touch probes: precisely sense part geometry at high contact pressures.
In essence, 45 steel is often used for load-bearing components where an optimal balance of properties is required. 40Cr steel is generally preferred for cutting/fixture components that undergo intensive surface wear and can take advantage of induction hardening for case hardening. The specific component, design loads, and application ultimately dictate the best material selection.