Metal Groove Machining Guide: Metal Grooving Process Methods, Tools, Challenges & Solutions
The machining process that creates grooves through cutting is called “groove machining.” In metalworking, the design of the part dictates the types of grooves, each requiring different machining methods. To perform precise groove machining, it is important to understand the characteristics of each type of machining and the points of caution during the process. This article introduces the features of groove machining, the tools used, and the challenges and solutions during machining.
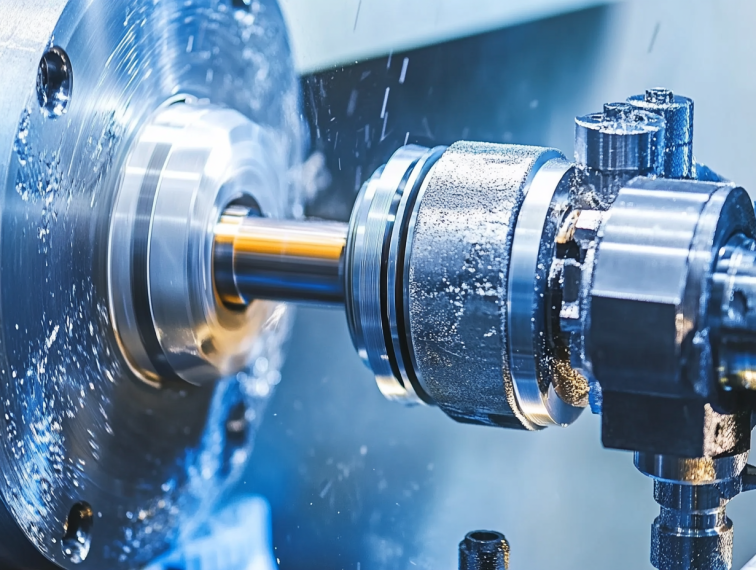
What is Groove Machining?
Groove machining involves carving grooves into a workpiece according to the design of the part. It is used to position parts relative to each other and to provide locations for mounting components. For example, when attaching another part to a rotating shaft, simply threading the part onto the shaft and fitting it in place can lead to slippage due to inertia and the load during rotation. However, if grooves are machined into both the rotating shaft and the part to be attached, they can be fixed securely together, preventing slippage. Thus, groove machining plays a vital role in transmitting rotational forces and securely assembling parts.
Groove Machining Methods & Tools
Groove machining can be categorized into several types based on the shape of the groove and its purpose, such as keyway machining, T-slot machining, dovetail slot machining, and spline machining.
Machines like milling machines, machining centers, slotters, and broaching machines are used for machining, each requiring different cutting tools and methods. This section introduces the characteristics of typical groove machining and the cutting tools used in milling machine operations.
- Keyway Machining
Keyway machining creates a “keyway” slot in the internal and shaft diameters for fitting machine parts. The cross-section of a keyway is rectangular, which prevents the fitted parts from shifting. Although it is useful for positioning during assembly, cutting out parts to create a groove can lead to reduced strength and increased risk of damage due to stress concentration. When using a milling machine, side mills, slot mills, and end mills are employed. Using an end mill for keyway machining can evenly distribute the load on the cutting edge by either reducing the vertical cutting depth gradually or moving the end mill laterally in an arc. - T-slot Machining
The “T-slot” has a cross-section that looks like an inverted “T.” It allows for the head of a bolt or nut to be inserted at the wider bottom part for securing with screws. Like keyway machining, a single groove is carved using side mills or end mills on a milling machine, followed by a “T-slot cutter” to process the wider bottom part. - Dovetail Slot Machining
Unlike a T-slot, a dovetail slot appears like an inverted “Y” with a flat base, used in positioning stages and cylinders as a guide mechanism. A “dovetail slot mill” is specifically used for its machining. - Spline Machining
This involves machining grooves on the outer circumference of a rotating shaft or the inner circumference of a part to be fitted, allowing for spline engagement. Due to multiple rectangular keyways being machined, spline connections can provide high strength. Splining is typically done using slotters or broaching machines.
Challenges and Solutions in Groove Machining
Groove machining, which involves creating non-through shapes, can pose unique challenges such as reduced machining accuracy, tool life, and poor chip removal. This section explains these challenges and their solutions.
- Reduced Machining Accuracy
Methods like one-shot grooving, aimed at increasing productivity, do not involve finishing the machined surface, which can lead to reduced finish quality and continuous defects. Vibration, particularly when machining deep grooves, is a common cause of reduced accuracy. Using highly rigid carbide cutting tools or tools with short protrusions can mitigate this. - Tool Life Reduction
Deep groove machining places high stress on cutting tools, reducing their life. To extend tool life, improvements in chip removal, the use of high-performance coolants, and coating revisions are necessary. - Poor Chip Removal
In deep groove machining, chips can accumulate at the deepest part of the groove, potentially leading to reduced machining accuracy. Ensuring proper coolant supply and adjusting cutting conditions are critical for effective chip removal. Slot mills may offer better chip removal than end mills.
Representative Methods of Keyway Machining
Keyway machining can also be performed using tools other than end mills and mills. This section introduces typical methods and their features.
- Slotter Machining
This involves using a cutting tool attached to the spindle of a machine tool that moves up and down to gradually carve out an internal keyway. Also referred to as vertical shaper machining, it allows for high flexibility in processing various shapes and sizes and stopping hole machining. However, the process is time-consuming, making it less suitable for mass production. - Broaching
Using a specially designed broach to shape the internal diameter, the keyway is completed by pulling the broach through the part. Broaching is quick and offers consistent accuracy, making it ideal for mass-produced items. However, it is not suitable for creating stop holes. - Keyseater Machining
Suitable for machining large products with wide keyways or large external diameters. Other methods like electrical discharge machining (EDM) and wire cutting can also create keyways.
Selecting Appropriate Machining Methods and Cutting Tools
Groove machining is an essential process in machine part production. However, due to the nature of the groove shape, it is prone to issues like vibration and poor chip removal, leading to decreased machining accuracy and tool life. Selecting the right machining methods and cutting tools is crucial to enhance both efficiency and accuracy.