The Shell Processing Technology & Mold Design Of The Floor Scrubber
With the improvement of living standards, people are increasingly emphasizing the cleaning effect and appearance design of floor scrubbers. As a component that users directly come into contact with, the quality and appearance of the floor scrubber shell directly affect the product impression. This article will explore in detail the processing technology and mold design of the floor scrubber shell, focusing on the bottom shell design (hot runner mold), silver stamping process (ultrasonic welding), pillar back shell mold design, chassis cover mold design, and scraper process.
1.Mold design for the bottom shell of the floor scrubber
The bottom shell of the floor scrubber is produced using a hot runner mold, which is suitable for forming large-sized plastic parts. Hot runner molds perform excellently in maintaining the fluidity of plastic melt, ensuring uniform distribution of materials within the mold and avoiding product deformation or incomplete filling. Although the initial cost of hot runner molds is relatively high, it significantly reduces overall production costs by reducing material waste, shortening production cycles, and improving product surface quality. Due to the large size of the bottom shell of the floor scrubber, using a hot runner mold can ensure a smoother flow of plastic in the mold, avoiding the potential cold spot problem caused by the cold runner system. In addition, hot runner molds can reduce gate residue and further improve appearance quality.
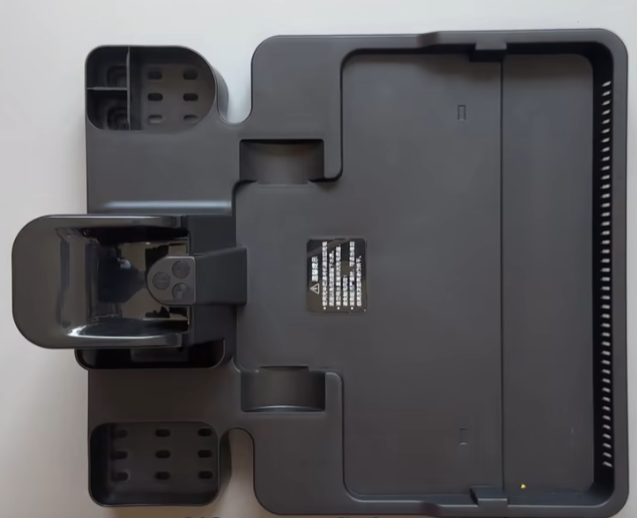
The benefits of hot runner molds
Realize one-time molding of complex components. Hot runner molds utilize the principle of rapid fluid cooling to achieve complex internal and external structures of hard parts in a single casting, avoiding the need for multiple processing.
Short molding cycle and high production efficiency. Compared with traditional molds, hot runner molds ensure rapid fluid flow, shorten solidification time, and significantly improve production efficiency.
The molding quality is stable and reliable. Rapid circulation and uniform solidification can obtain excellent material structure and density distribution, improving the surface smoothness and dimensional accuracy of the product.
Save materials and reduce costs. Compared with multiple processing, one-time molding can minimize molding failures, save material investment and costs.
Suitable for the production of complex components. Suitable for large-scale production of complex internal and external components that require one-time molding, such as wheel frames, gearbox housings, etc.
Flexible modification. Simply modify the mold flow channel or size to achieve the molding of different products, making modification convenient and fast.
The product quality is reliable. The rapid and uniform solidification can ensure the delicate structure and mechanical properties of the product.
2. Marking and ultrasonic welding of the floor scrubber shell
Ultrasonic welding technology is widely used in the connection of floor scrubber shell components. This technology utilizes high-frequency vibration to generate local heat at the interface of plastic parts, causing the plastic to melt and achieve a secure connection. Ultrasonic welding has the advantages of high precision, short cycle, and no need for additional adhesive, making it very suitable for products such as floor scrubber casings that require aesthetics and good sealing.
In the processing of floor scrubber shells, ultrasonic welding is not only used for connecting parts, but also combined with silver stamping technology. The silver stamping process involves heating a mold to transfer metal foil onto a plastic surface, resulting in exquisite patterns or logos. This process not only enhances the visual effect of the product, but also enhances its brand value.
3. Design of the mold for the rear shell of the column
As an important part of the structure of the floor scrubber, the rear shell of the column requires special attention to the setting of reinforcement ribs in the mold design. Normally, PP materials are designed with a reinforcing rib thickness of 30% of the wall thickness to prevent shrinkage on the exterior surface. At the same time, to ensure structural strength, the minimum thickness of reinforcing bars cannot be less than 0.5mm.
If the thickness of the reinforcing rib exceeds 30% of the wall thickness and the appearance requirements are high, adjustments need to be made in the subsequent injection molding process. For example, by optimizing the cooling rate, adjusting the injection speed, or adjusting the pressure setting, it is ensured that the ratio of wall thickness to reinforcing rib thickness remains within 40%, effectively avoiding shrinkage problems.
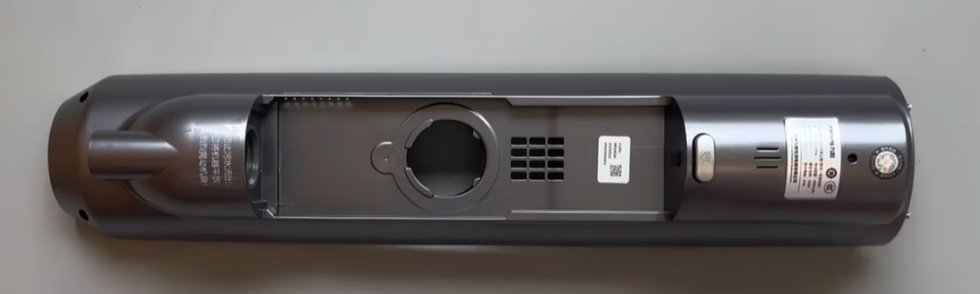
The benefits of strengthening reinforcement design
Improving structural strength and rigidity: Strengthening ribs can significantly enhance the structural strength and rigidity of plastic parts by increasing the thickness of materials or creating supporting structures, preventing deformation and warping, and enhancing overall durability.
Weight reduction: Compared to directly increasing wall thickness, reinforcing ribs can provide additional support without significantly increasing material usage, achieving the goal of reducing part weight, especially suitable for products that require lightweight design.
Reducing material costs: By optimizing the design of reinforcement bars, the use of materials can be reduced and production costs can be lowered without affecting structural performance. This is particularly important for plastic parts produced in large quantities.
Improving appearance quality: Reasonably designed reinforcing ribs can avoid or reduce defects such as shrinkage and indentation on the surface of plastic parts, thereby improving appearance quality. This is crucial for products with high appearance requirements.
Enhance product durability: Reinforcing ribs can disperse stress, reduce concentrated stress points, thereby improving the impact resistance and fatigue resistance of the product, and extending its service life.
4. Design of chassis cover mold
The chassis cover is an important protective component of the floor scrubber, and its mold design directly affects the durability and appearance quality of the product. When designing, it is necessary to comprehensively consider factors such as mold polishing treatment, part assembly clearance, and production efficiency.
The polishing treatment of the chassis cover mold is particularly crucial, as it directly determines the surface smoothness of the final product. High quality polishing treatment can not only improve the aesthetics of the product, but also reduce dust adhesion and enhance the cleaning effect. In addition, mold design should also ensure that the assembly clearance of the parts is moderate, ensuring that there is no stress concentration during the assembly process and extending the product’s service life.
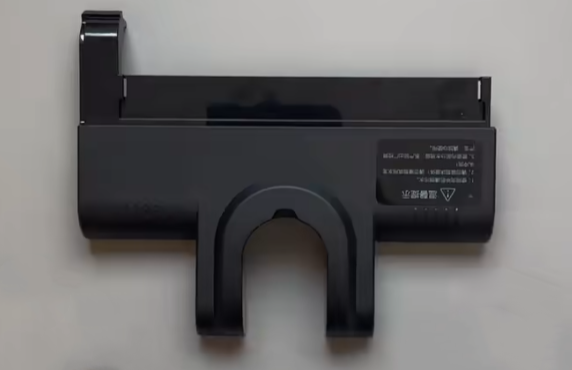
5. Scraper process
The scraper is the cleaning component of the floor scrubber, and its process design directly affects the cleaning effect. Usually, the design of scrapers requires high wear resistance and good flexibility in order to adhere closely to the ground during use and achieve optimal cleaning results.
During the manufacturing process, the material selection and forming process of the scraper must be strictly controlled. The material is usually made of wear-resistant rubber or composite materials, processed through precision mold forming technology. At the same time, the size and shape design of the scraper should match the movement trajectory of the entire machine to ensure maximum cleaning coverage and effectiveness.