What is Linear Motor? Principle, Structure, Pros, Cons, Types, Applications in CNC Machine Tools
A motor called a linear motor is making quite an impact in packaging industries and CNC machines. When someone says motor, the image that comes to mind is usually something spinning. However, packaging and CNC machines require motors with linear movement. Linear motors obtain thrust force through non-contact driving, and are effective for high-speed movement, high-precision machining, low vibration, and low noise. Therefore, they are used in a wide range from large applications like high-speed rail (linear motor cars), amusement park attractions, high-speed elevators, monorails, to small applications like machine tools, semiconductor manufacturing equipment, industrial conveyance systems, and drive units for precision instruments. In this article, we will introduce the principles and structure of linear motors, as well as application examples in machine tools.
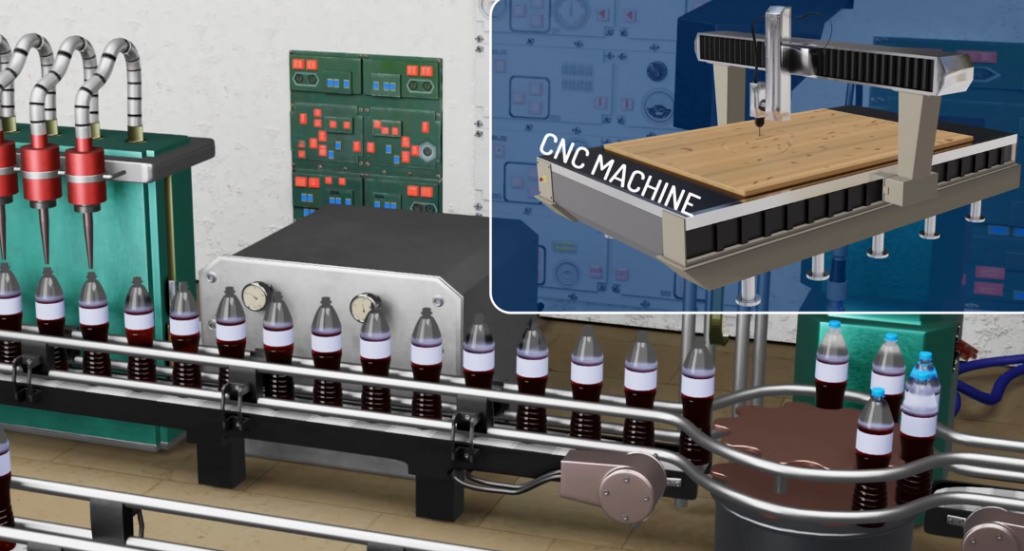
1. What are Linear Motors? Principles and Structure
Linear motors are electric motors whose rotating motors are stretched out in a linear shape. While common motors have a rotating shaft and exhibit rotational motion, linear motors do not have a rotating shaft and exhibit linear motion along rail-like tracks like trains.
Below, I will explain the principles and structure of linear motors.
(1) Principles
The principles of linear motors are mainly three: propulsion, levitation, and induction.
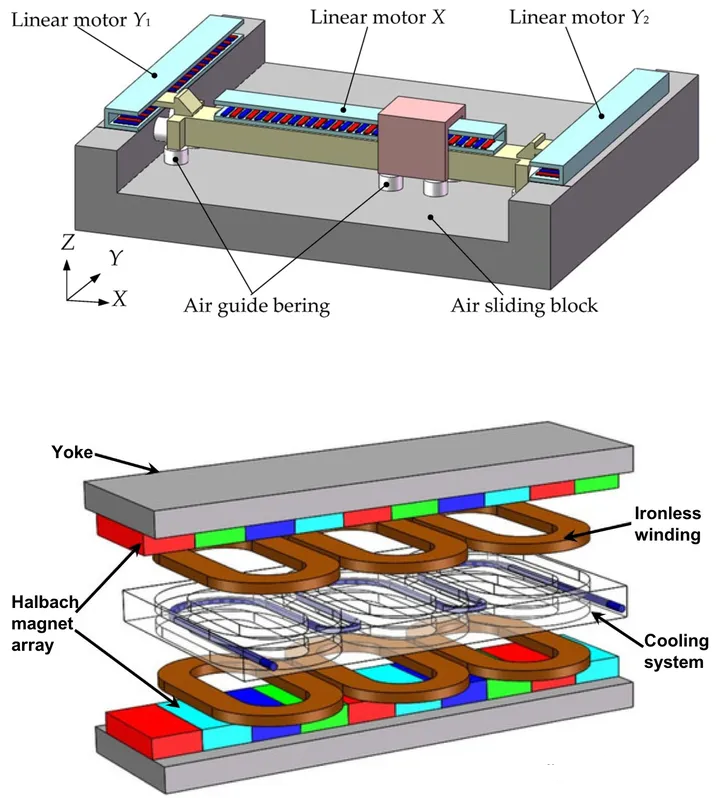
- Propulsion
By alternately arranging N and S poles of magnets in a straight line and flowing current to generate a magnetic field, propulsion force is obtained through the attractive and repulsive forces between the N and S poles. - Levitation
Levitation is achieved through the repulsive forces between like poles of magnets – N to N and S to S. - Induction
The interaction between N and S poles is also utilized for position measurement. If the object shifts to either side of the set position, the farther side is pulled by the attractive force of the magnets while the closer side is pushed back by the repulsive force, so the object always returns to the center.
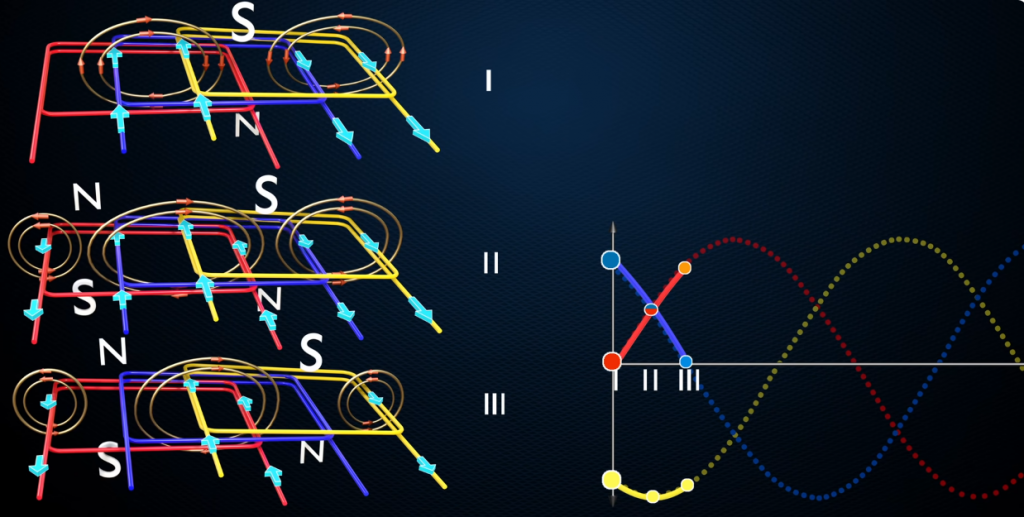
(2) Structure
The basic structure of a linear motor involves fixing magnets on a base and alternating N and S poles of the magnets. Current is then flowed through coils (movers) placed above the magnets to generate a magnetic field, moving the object incorporating the coils.
When used in machine tools, linear servo motors are commonly installed in table or shaft types and used in combination with linear motor guides.
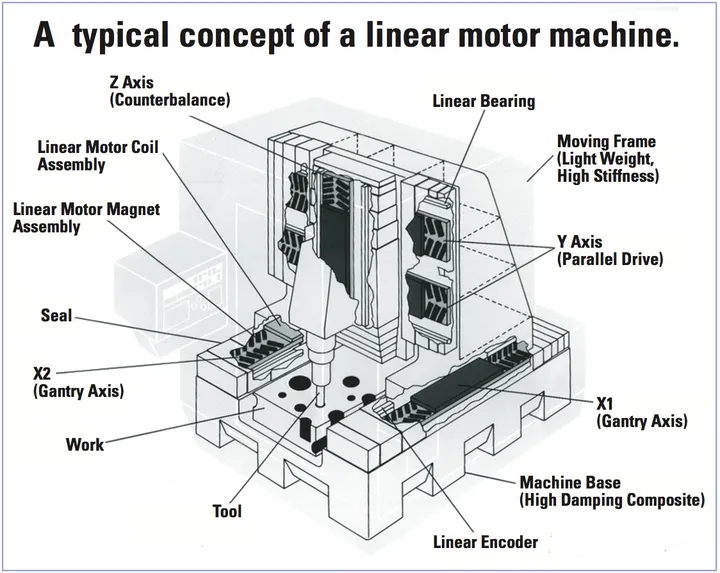
Servo motors are motors used for purposes like position and speed control. A program is installed in a driver which provides operation control instructions to the servo motor, and the servo motor’s operation is controlled by sending electric signals from the driver.
2. Advantages and Disadvantages of Linear Motors
Below I will introduce the advantages and disadvantages when linear motors are used in machine tools.
(1) Structural Advantages
There are mainly the following six structural advantages:
- High assembly accuracy without speed reducers enables high-precision reciprocating motion
- No wear parts like ball screws and nuts, resulting in less deterioration
- No length limitations, can be extended as much as needed
- No installation space needed for rotating motor parts, allowing compact design
- Multiple motors can be arranged on the same axis, movable together or separately
- Less maintenance required due to fewer machine parts
In addition, linear motors can maintain a non-contact state through the repulsive force of magnets. Therefore, they have the following advantages compared to contact parts like ball screws and nuts for linear motion:
- Motor rotational force does not deteriorate even after long-term use, continuously transmitting correct force to the machine
- No shaft runout or distortion
- Less metal fatigue and deterioration
- Almost no consumable parts
Linear motors satisfy these conditions, so they can maintain high accuracy even after long-term use. They also eliminate the length limitations of ball screws in machine tools, enabling the production of long stroke axes.
(2) Speed Advantages
Linear motors used to have the disadvantage of being susceptible to external influences, but manufacturers have worked on mechanical design improvements to suppress factors like linear guides, electrical noise, and mechanical resonance, resulting in structures that are now less affected. Also, the friction resistance at contact parts with conventional rotating motors and ball screws limited high speed rotation, but linear motors have no friction resistance due to their non-contact nature, enabling high speed rotation and movement.
Therefore, they have the following speed advantages:
- Enable high speed rotation, positioning, and other high speed movement
- High precision enables high speed operation, improving work efficiency
These advantages have led to adoption in industrial robots, inspection equipment, and other applications requiring accuracy and work efficiency.
(3) Environmental Advantages
The use of mineral oils in conventional hydraulic equipment raises the following two concerns:
- Environmental pollution from waste oil disposal
- Adverse health effects from oil use on humans
Replacing such equipment with linear motor-equipped machinery provides the following advantages:
- Minimizes the use of oils
- Reduces waste oil volume
- Uses electricity and magnetism, reducing oil use and impact on humans
- Reduces environmental pollution from waste oil disposal
While most waste oil is recycled into products like soap, candles, and rerefined heavy oil, chlorinated metalworking oils cannot be reused and must be disposed of through incineration or landfilling, potentially causing CO2 emissions and soil contamination. Using linear motors minimizes mineral oil use, also reducing waste oil volume and allowing environmental considerations.
Advances in downsizing technology also enable replacing large conventional equipment with compact linear motor machines, saving space.
(4) Disadvantages and Cautions with Linear Motors
The main disadvantages and cautions with linear motors are:
- Large force required to move linear motors
Without speed reducers, linear motors cannot produce large forces like rotating motors and ball screws in small sizes. Therefore, high output requires large equipment, with compact high output design remaining an engineering challenge. - Environmental measures necessary for use
When used in machine tools, factors like metal and resin chips and cutting oil scatter can damage linear motor sections. Countermeasures include adopting linear motors with higher oil resistance and installing protective covers to prevent damage from chips and oils. - Workpiece deformation from heat generation during operation
With grinding machines, rotation at higher outputs than conventional rotating motors and ball screws can potentially deform workpieces from heat generation during operation. To prevent deformation, linear motors with low heat generation must be adopted or cooling devices installed. - Precise control required
Linear motors are susceptible to external disturbances, making control difficult and requiring precise control for high precision machining. Effective countermeasures include high-gain servo motors, increasing structural resonance frequencies, and separate control against disturbances. - May be unable to use with existing equipment
Machine tool specifications differ by application, so linear motors may be unable to be used with existing equipment. When partially replacing existing equipment with linear motor machines, custom fabrication may be necessary even for the same output due to incompatible standards. With existing linear motor machines, little compatibility can be expected between different manufacturers, forcing reliance on the same manufacturer.
3. Types of Linear Motors
There are various types of linear motors, five of which are introduced below.
(1) Linear Synchronous Motor
Linear synchronous motors (LSM) use coils arranged in a straight line and conductive movers with magnetism that move along them. Generating a magnetic field by flowing current in the coils causes the mover to move linearly following changes in the magnetic field. Features include efficient energy use with little loss due to the induction principle and no rotating parts with quiet operation and relatively easy control. Their linear motion enables use in various fields including high-speed rail, monorails, elevators, and industrial machinery.
(2) Linear Induction Motor
Linear induction motors (LIM) also enable linear motion but with a different principle from LSMs. They consist of coils arranged in a straight line and conductive movers (aluminum, copper, etc.) with flowing current above the coils. The mover magnetic field interacts with the alternating magnetic field from the coil current to produce linear propulsion force. Their linear motion enables use in transit systems, industrial machinery, and conveyors.
(3) Linear DC Motor
Linear DC motors (LDCM) use direct current to produce linear motion, typically consisting of a stator with coils and a rotor with permanent magnets. Flowing DC current in the stator coils produces a magnetic field that interacts with the permanent magnets to linearly move the rotor, enabling attached machines or objects to move linearly. Precision linear motion applications include custom industrial machinery, robot arms, medical equipment, and industrial machinery.
(4) Linear Resonant Actuator
Linear resonant actuators (LRA) are actuators like motors or cylinders that convert electrical energy, hydraulic pressure, pneumatic pressure, etc. into motion. Basic structures include conductive coils, permanent magnets, springs, and vibration plates inside the actuator. Coil current produces a magnetic field that applies force to the springs and vibration plates, causing vibration. Features include vibration of various objects, fast response, and tactile feedback like direct touch. Applications include smartphones, touchscreens, game controllers, and home appliances.
(5) Linear Electrostatic Motor
Linear electrostatic motors utilize electrostatic principles, typically consisting of moving and fixed electrodes using electrode films or plates with embedded strip electrodes. Multiple alternating layers of moving and fixed electrodes are stacked inside the housing. AC voltage in the electrode films charges the moving electrodes, causing machine/object motion from surrounding electrical field changes. However, high thrust linear electrostatic motors require preventing dielectric breakdown from AC current. The strong electric fields around the electrode films during 3-phase AC can cause dielectric breakdown. Immersing the electrode films in insulating liquid in a sealed state prevents breakdown but requires low-friction processing of the output shaft in the completely sealed state. The challenges to commercialization keep linear electrostatic motors at the experimental stage, but the lack of coils could enable lightweight, thin designs if realized.
4. Linear Motor Applications in Machine Tools
Here are 4 main examples of how linear motors are used in machine tools:
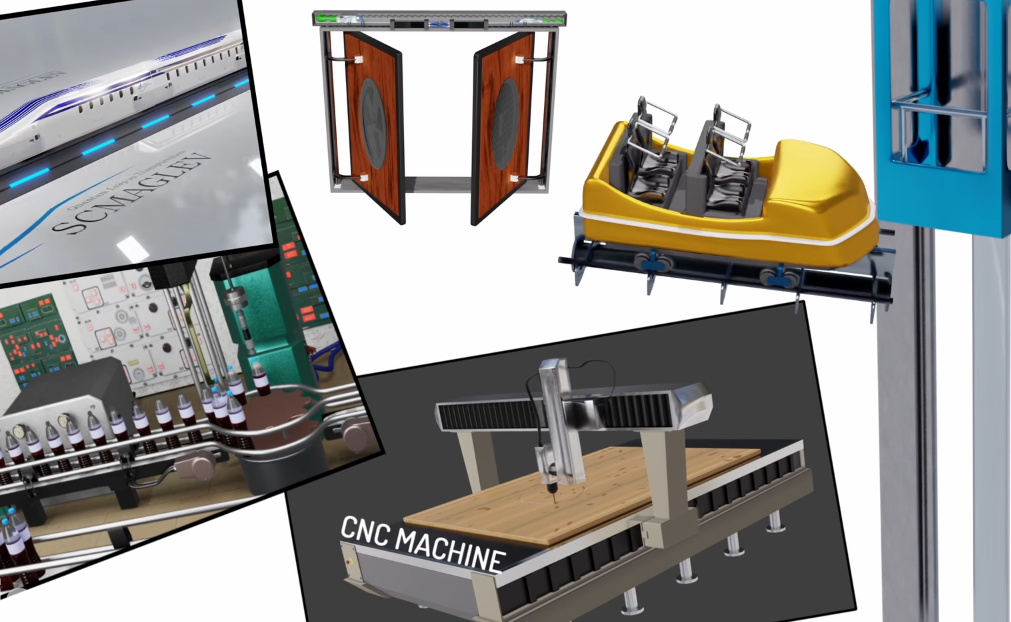
(1) Machining Centers
Linear motors can position with extremely high accuracy, so they are used to precisely control the location of tools and blades in machining centers, enabling continuous processes like grooving, milling, drilling, threading, and reaming. Machining centers come in vertical, horizontal, gantry, and multi-axis types depending on the application, but adopting linear motors in the drives improves accuracy, ease of maintenance, and work efficiency. Multi-axis controls like 5-axis machining centers can also complete a whole part in one setup if the programming is correct, allowing highly efficient work. However, with more work steps, careful programming of the control is necessary.
(2) Cutting and Grinding Machines
Cutting and grinding machines require high precision and faster cycle times, so linear motors help improve efficiency beyond what ballscrews and rotary motors can achieve. They are adopted in the drives of these machines. Being non-contact, linear motors avoid the wear of ballscrew and rotary motor contacts, and can be used for long periods with just consumable replacement. One caution is that the heat from high speed rotation can deform the workpiece, so cooling systems should be designed into cutting/grinding machines or added separately.
(3) Electrical Discharge Machines
Linear motors and linear scales enable high speed, high precision machining and quick response. With accurate programming, operation is simplified so even amateurs can work them. As with cutting/grinding machines, the heat can deform the workpiece, so cooling systems need consideration.
(4) Spinning Machines
Spinning machines form sheet metal against a rotating mandrel using a forming roller. Linear motors drive the forming roller. With the mandrel fixed, the roller can be precisely positioned by the linear motor. Moving the roller parallel to the mandrel forms the same shape. Linear motors enable shaped sections like polygons and eccentrics that would be difficult with conventional drives, removing the need for skilled operators.