What is Tap: Types, Applications, How To Clean & Remove
Taps are divided into four types: extrusion taps, spiral taps, straight groove taps, and tip taps, each suitable for different situations and materials. Today we will explain the precautions for using a tap, including cleaning materials, selecting the appropriate type of tap, and using the tap correctly.
The Type of Tap
Squeezing tap
The body of the drill bit gradually tapers from the head to the tail, forming a cone. The thread pitch gradually increases from the head to the maximum at the tail. Due to the increase in thread pitch, the cutting cone angle at the tail is greater than that at the head. This design enables the fine threads on the head to effectively initialize the guide hole and remove material debris during the drilling process. The thick threads at the tail can efficiently cut and stir materials, accelerating the feed rate. It is mainly suitable for drilling soft materials such as plastic, cork, rubber, etc. Due to its conical impurity removal function, it can effectively advance in soft materials, remove chips, and shorten drilling time.
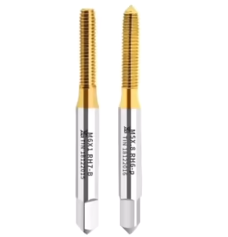
Spiral tap
The shape is conical, gradually becoming thinner from the cylinder to the tip, with the largest diameter at the head and the smallest at the tail. There are evenly distributed threads on the surface, and compared to other types of taps, the thread spacing is relatively small, with more threads per inch, usually between 3-12 threads per inch. Due to the dense threads, each round of threads can more effectively cut and remove material debris from the material, and the drill bit has strong rigidity and support capacity. The main application is primary drilling, such as drilling guide holes in harder materials such as steel and gypsum boards. Due to the dense threads and strong structure, it can quickly and effectively open guide holes. Proper rotation speed and feed force are required for use. High speed can give play to its advantages of rapid cutting, and the feed force needs to be moderate, which can not only cut fast but also ensure the circularity of the hole diameter.
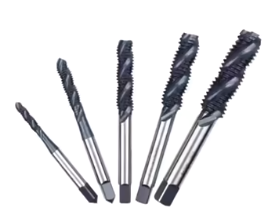
Straight flute taps
The shape is conical, similar to a regular thread tap, but with a straight groove on the surface. The distribution of straight grooves is uniform, and usually there is a straight grove between each thread. A straight groove can effectively remove and discharge drilling debris and shavings generated during the drilling process. It is suitable for drilling holes that require deep or strong penetration. More suitable for handling materials with medium to hardness, such as wood, plastic, non-metallic materials, etc. When using, the drill bit should be kept perpendicular to the working surface and rotated and pushed at a uniform speed.
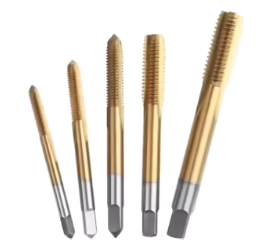
Leading tap
The drill bit has a conical shape, but the top of the cone is slightly flat, forming a small plane. This flat part has no threads and the top surface is smooth in the shape of a disc. The threaded structure can only be arranged from below the plane. When the leading tap is drilled into the interior of the working material, the flat top structure can effectively remove the cut material. Prevent chips from blocking the hole and affecting the feed. After entering a certain depth, the thread below begins to work and the rotary cutting completes the through operation. So, the leading tap is specifically designed for hole positions that require complete penetration. For example, in applications such as drilling through holes in wood or metal plates. Compared to ordinary cone designs, it has better results in removing chips and is suitable for situations where cutting needs to be completed in deep areas.
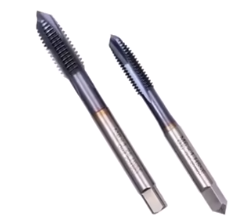
The Application of Tap
1. Manufacturing and mechanical processing
In the manufacturing industry, taps are widely used to process internal threads of various parts. Typical applications include:
Automotive components: threaded holes in engines, transmissions, and suspension systems.
Aerospace: Precision threading of aircraft and spacecraft structural components.
Industrial equipment: threaded connectors in pumps, compressors, and industrial machinery.
Household appliances: Internal threaded connections in washing machines, refrigerators, and air conditioners.
2. Architecture and Civil Engineering
Taps are used in construction and civil engineering to create threaded holes for fixing and connecting structural components. For example:
Steel structure building: bolt holes for connecting steel beams and columns.
Bridge construction: Processing of threaded holes for bridge support and connecting components.
Pipeline engineering: threading of pipeline connections and fixing devices.
3. Repair and maintenance
Taps also play an important role in equipment maintenance and repair, often used to repair damaged threaded holes and create new threads. For example:
Mechanical equipment maintenance: repair worn or damaged threaded holes to ensure the normal operation of the equipment.
Automotive repair: Create or repair threaded holes in the engine and other components to ensure secure connections of fasteners.
Household appliance maintenance: repairing or replacing threaded connectors in household appliances.
4. DIY and Handmade
For DIY enthusiasts and handmade projects, taps are also commonly used tools for thread processing on various metal and plastic materials. For example:
Furniture making: Create threaded holes in metal or wooden furniture components to ensure secure connections between the components.
Model making: Create fine threaded connections in both model and prototype making.
5. Electrical and electronic equipment
In the manufacturing and assembly process of electrical and electronic equipment, taps are used to process threaded holes for various connecting components. For example:
Electrical housing: Create threaded holes on metal or plastic housing to secure panels and components.
Electronic device assembly: Create threaded holes on the circuit board and device casing to ensure stable connection of fasteners.
How to Remove a Broken Tap
1. Use a tap extractor
A tap extractor is a specially designed tool for removing broken taps from holes.
Choose the appropriate extractor: Select the appropriate tap extractor based on the size of the broken tap.
Insert extractor: Insert the claw of the extractor into the threaded groove of the broken tap.
Rotate the extractor: Rotate the handle of the extractor clockwise until the broken tap becomes loose and removed.
2. Use Electrical Discharge Machining (EDM)
Electrical discharge machining (EDM) is a non-contact machining method that uses electrical discharge to remove metals, especially suitable for hard materials and precision machining.
Positioning: Fix the workpiece on the EDM equipment, ensuring that the broken tap is located in the discharge area.
Set parameters: Set appropriate electrical discharge machining parameters based on the material and tap size.
Processing: Start the EDM equipment and use electric spark to remove the broken tap. During the processing, it is necessary to maintain a stable discharge gap and cooling.
3. Use drill bits and drilling machines
This method is suitable for situations where the broken part of the tap is exposed on or near the surface of the workpiece.
Choose a drill bit: Choose a hard alloy drill bit with a diameter slightly smaller than the diameter of the broken tap.
Drilling positioning: Drill a small hole in the center of the broken tap to provide guidance for the drill bit.
Drilling: Align the drill bit with the small hole, slowly drill in the broken tap, and try to remove it as much as possible without damaging the threaded hole.
Use reverse rotation drill bits: If there are specialized drill bits with reverse rotation, they can be used to help remove broken taps.