Why Use Eagle Beak Gating for Deep Cavity Mold Products & Processing Considerations
The primary reason for using eagle beak gating for deep cavity products is to optimize the gating system design, thereby improving product molding quality and production efficiency. Eagle beak gating can effectively control the direction and speed of the melt flow, reducing backflow and uneven cooling within the mold, thus preventing issues such as warping and deformation of the product.
What is Eagle Beak Gating?
In mold design, eagle beak gating refers to a specific gating method commonly used in die casting molds. This method guides the molten metal into the mold through a gate shaped like an eagle’s beak, achieving uniform distribution and filling of the molten metal. Despite its advantages, eagle beak gating also has drawbacks such as susceptibility to erosion and significant kinetic energy loss, necessitating adjustments and optimizations in practical applications.
Processing Considerations for Deep Cavity Products
When processing deep cavity products, attention must be paid to the following aspects:
- Centerline Coaxiality: Ensure the coaxiality of the main spindle and the tool guide sleeve, tool holder support sleeve, and workpiece support sleeve to meet requirements for machining accuracy.
- Cutting Fluid System: Maintain a smooth and normal cutting fluid system to effectively cool and lubricate, preventing tool wear and workpiece overheating.
- Chip Formation: Avoid generating long ribbon-like chips to prevent tool damage and workpiece surface scratches.
- Chip Evacuation: Deep cavity processing involves small and deep holes with long chip channels, which can easily cause deflection, vibration, and breakage, affecting hole accuracy and surface quality.
- Tool Selection: Choose the largest possible tool within the machine’s maximum load to improve machining efficiency and quality.
- Design Phase Planning: Reasonably plan the cavity depth during the design phase, considering part structural strength, machining processes, and subsequent processing steps to determine the appropriate cavity depth range.
These measures can effectively enhance the machining quality and production efficiency of deep cavity products.
Technical Principles of Using Eagle Beak Gating for Deep Cavity Products
Eagle beak gating involves guiding the molten metal along the direction of the eagle beak into the mold. This method can better control the flow direction of the molten metal, ensuring it fills the deep cavity mold uniformly and quickly. The AnyDESIGN HPDC v1.1 software supports fully parametric design of eagle beak gates, allowing users to complete gate designs in a matter of seconds.
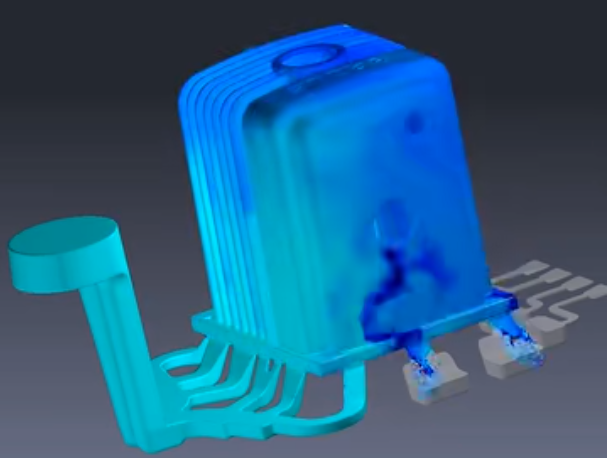
Controlling Centerline Coaxiality in Deep Cavity Machining
Accurate measurement and control of centerline coaxiality are crucial for ensuring machining precision in deep cavity machining, requiring various methods and techniques. Here are the detailed steps and methods:
- Selecting Appropriate Measuring Tools:
- Micrometer: Used to measure the diameter, roundness, and coaxiality of parts.
- Coordinate Measuring Machine (CMM): Provides high-precision measurements, suitable for complex shapes and small-sized parts.
Determining Reference Axis: Establish a reference axis as a basis before measuring coaxiality.
Measurement Methods:
- Indicator Measurement: Use micrometers or dial indicators to measure the deviation between the measured axis and the reference axis.
- Ultrasonic Measurement: For deep hole machining, use ultrasonic to measure wall thickness, calculating diameter, roundness, coaxiality, and straightness.
Marking Coaxiality Tolerance: Ensure the measured and reference elements are both central elements (axis).
Error Analysis: Analyze the main factors affecting coaxiality, such as the position of the center of the measured elements and the direction of the axis.
Comprehensive Evaluation: Consider roundness, straightness, and other geometric tolerance parameters for a thorough assessment of machining accuracy.
Optimal Configuration of Cutting Fluid System in Deep Cavity Machining
To ensure machining accuracy, extend tool life, and effectively reduce processing temperature, the cutting fluid system in deep cavity machining should adopt the following configuration schemes:
- Using Specialized Tools and Precise Cutting Fluid Solutions: Lower processing temperature, extend tool life, and improve machining accuracy.
- Semi-Dry Cutting Method: Employ a semi-dry cutting method with minimal cutting fluid, mainly using compressed air for chip evacuation and cooling.
- Optimizing Cutting Fluid Utilization Efficiency: Optimize the use of cutting fluid to achieve the best cutting effect.
- Setting Cutting Fluid Channels: In deep cavity small hole machining, set cutting fluid channels with sufficient pressure to enhance distribution and cooling.
- Mixing Cutting Fluid at Recommended Concentrations: Ensure uniformity and effectiveness of the cutting fluid.
- Selecting Suitable Lubricating and Anti-Rust Components: Provide good lubrication and anti-rust protection.
Solving Chip Evacuation Problems in Deep Cavity Machining
Effective solutions to chip evacuation problems in deep cavity machining to improve hole accuracy and surface quality include:
- Adjusting Cutting Parameters: Reduce the tool rotation speed and increase the feed rate to facilitate chip evacuation.
- Using Negative Pressure Chip Evacuation System: Design a multi-stage curved surface negative pressure chip evacuation system to enhance efficiency.
- Forced Cooling and Chip Evacuation: Use high pressure to deliver cutting fluid to the cutting area for cooling and lubrication, and chip evacuation.
- Selecting Appropriate Tools and Cutting Methods: Use positive rake angle cutting and choose tools with external helical chip grooves.
- Dry Milling with Air Blowing: In CNC milling, use compressed air and cutting fluid for dry milling and air blowing.
- Optimizing Coolant Nozzle Design: Aim the coolant nozzle at the hole to improve coolant entry into the cutting area.
Selecting Suitable Tools for Deep Cavity Machining
Selecting suitable tools for deep cavity machining requires comprehensive consideration of part structural strength and machining processes. Here are the detailed analyses and recommendations:
- Tool Type Selection:
- For deep cavity surface machining, fly cutters (e.g., D35R5 fly cutter) are a good choice due to their low cost and high efficiency.
- In high-speed machining, shorten the tool overhang as much as possible to reduce vibration and extend tool life.
Impact of Machine Type: Consider the type of CNC machine used, as different machines require different tool types (e.g., drills, turning tools, or milling cutters).
Material Characteristics: For materials like titanium alloys, which have high chemical reactivity, low elastic modulus, and high cutting temperatures, special attention should be paid to tool selection and machining strategies.
Tool Performance Requirements: CNC machines require high-quality tools; standard tools should be prioritized, and high-efficiency composite or special-purpose tools used when necessary.
Tool Parameter Settings: In practice, roughing tools can be initially selected with a diameter of about 35mm, a tool tip radius of 5mm, and a tool length of 150mm.
These methods and strategies can effectively enhance the precision and efficiency of deep cavity machining.